Products
- Home
- Products
High-Mix Low-Volume Precision Components
"High-Mix Low-Volume production is in the DNA of Tonasco, High Precision Machining is our passion!"
At Tonasco, every aspect of our operation is optimized for High-Mix Low-Volume series production of High Precision components. From high-end CNC milling machines and integrated IoT software to our layout and facilities, every element is tailored for efficiency and excellence in precision manufacturing.
Our state-of-the-art Tonasco Smart Factory boasts advanced machinery and cutting-edge machining technologies, including Simultaneous 5-axis CNC Milling Centres, CAM (Computer-Aided Manufacturing), and Simulation Software. These capabilities enable us to meet the most stringent demands for tight tolerance control with precision and reliability.
Superior product quality is our top priority and ultimate commitment to our high-tech clients. Our large team of highly trained QC technicians utilizes high precision QC instruments such as automated Zeiss Coordinate Measuring Machines (CMM) and Visual Inspection Machines. With an ISO9001:2015 certified quality management system and stringent In-Process Quality Control (IPQC) procedures in place, we consistently deliver high-quality components year after year.
Micromachining Precision Components
Micro-milling is at the heart of our expertise. From crafting micro-grippers and surgical robot parts to manufacturing medical-grade plastic gears, we specialize in producing high-quality micro-components ranging in size from 5 to 10mm, with precision tolerances as tight as ±0.005mm.
At Tonasco Smart Factory, we boast cutting-edge 5-axis and multitasking milling centers equipped with high RPM speeds and advanced tooling. Our 3D video measuring quality control systems are optimized specifically for micro-component production, ensuring meticulous attention to detail and precision.
Years of experience in micro-milling have allowed us to develop efficient machining strategies that optimize both time and cost without compromising quality. This is particularly crucial for small precision components that can pose handling challenges during and after machining.
Our well-established quality management systems and automated QC solutions, including First Article Inspections (FAI) and In-Process Quality Control (IPQC), guarantee consistent quality across every mix and series of components we produce. Leveraging smart setup techniques and advanced workpiece handling, we efficiently fabricate high-mix, multi-series orders ranging from 20 to 1000 quantity micro-components.
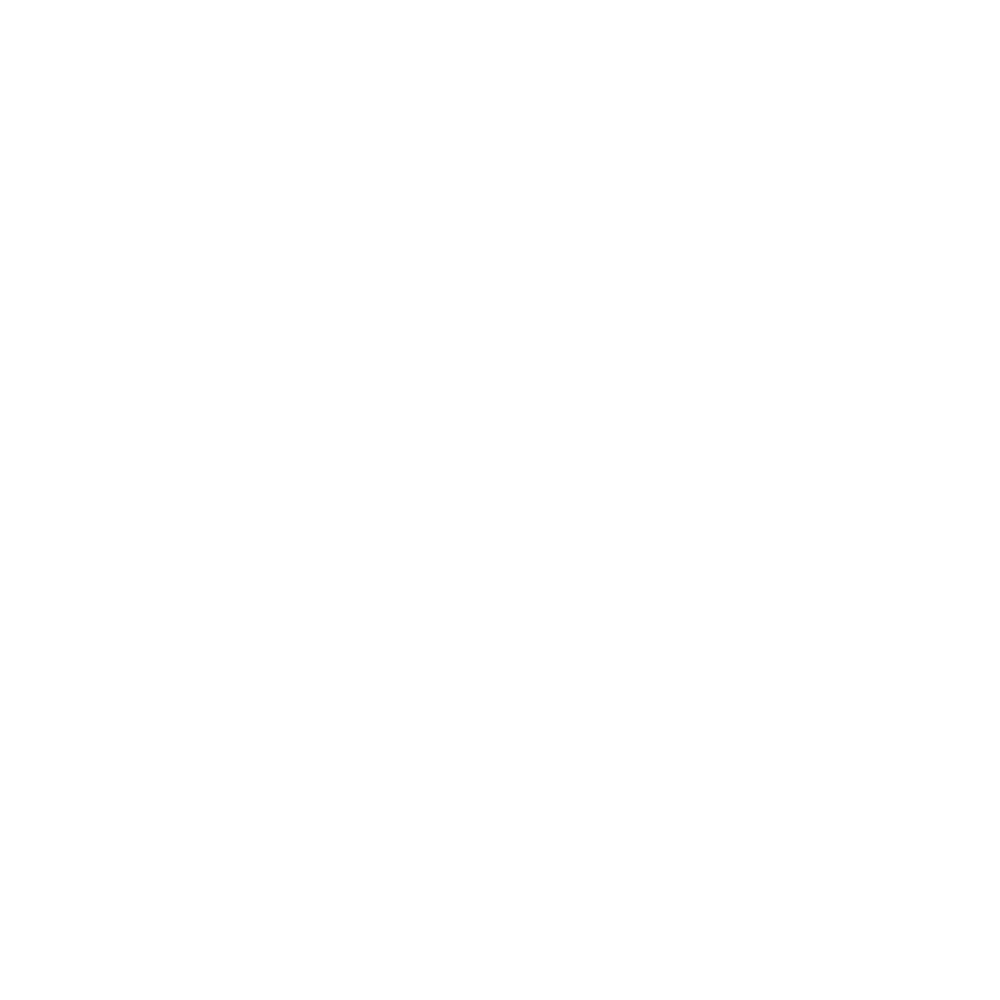
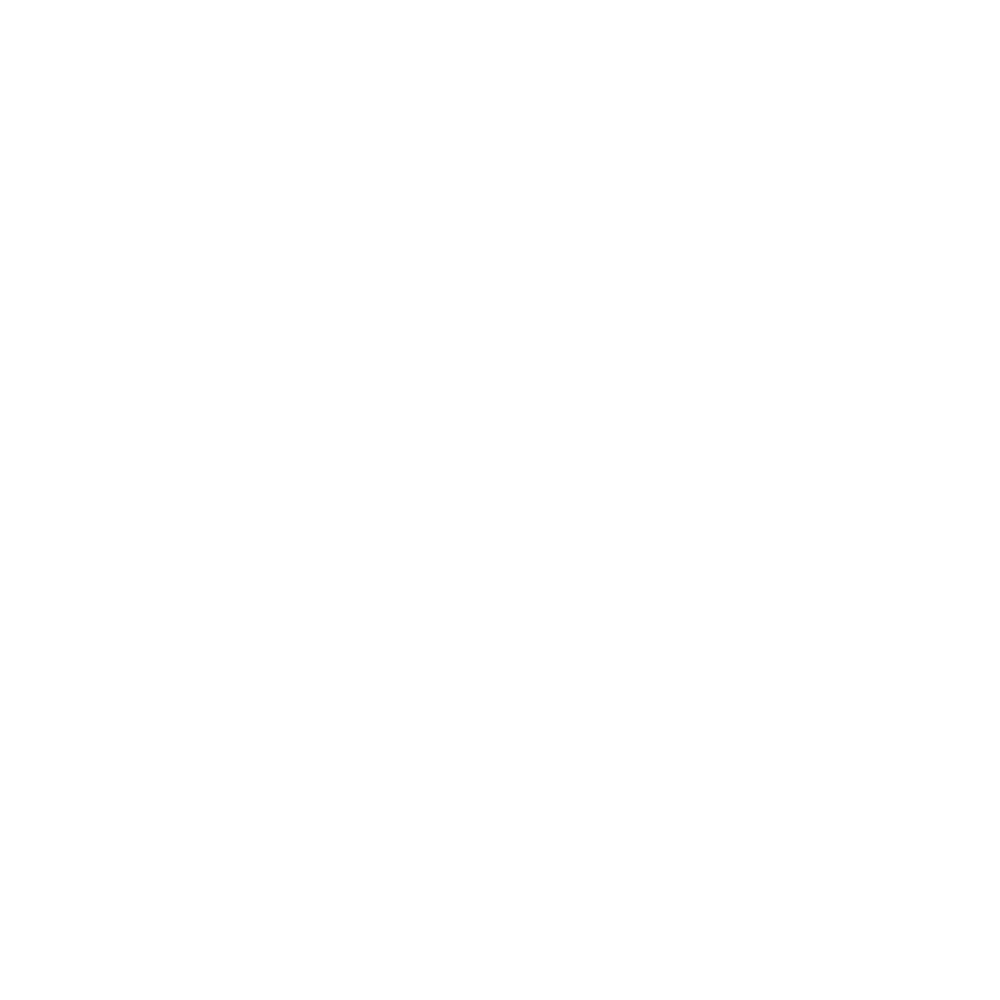
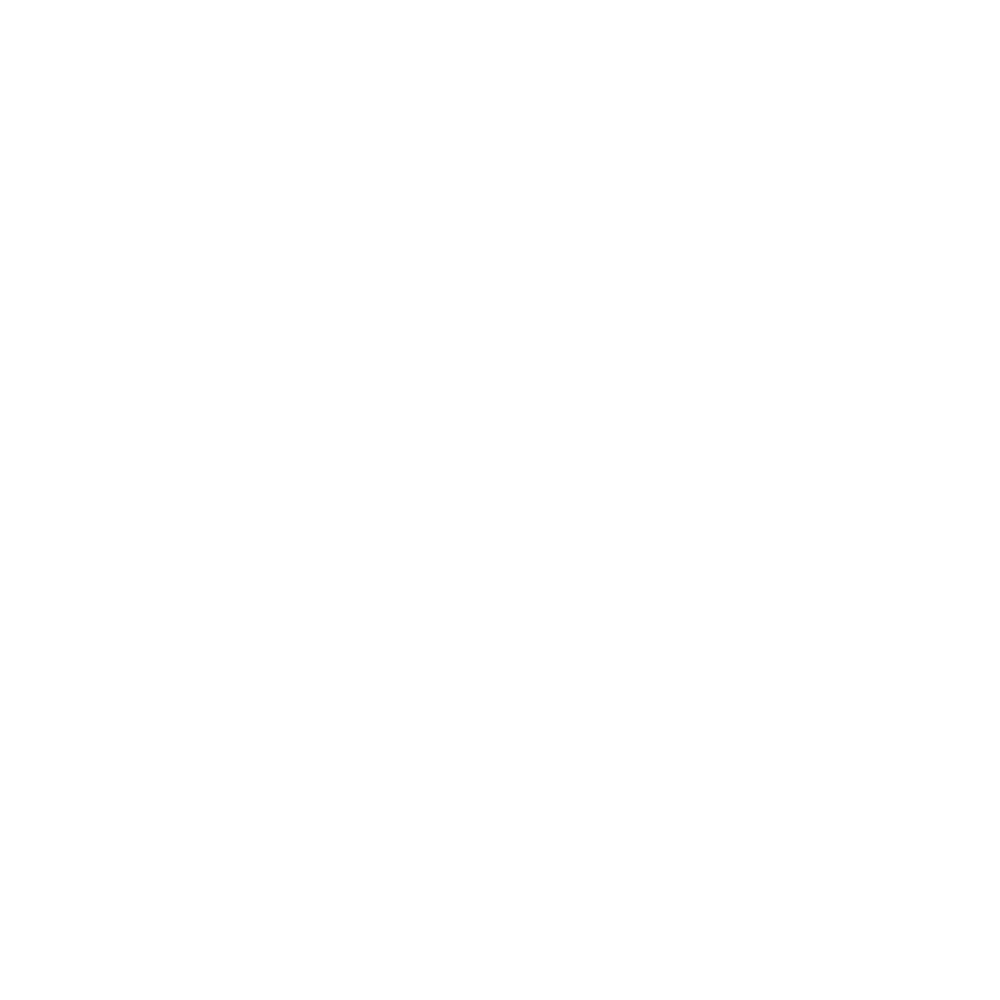
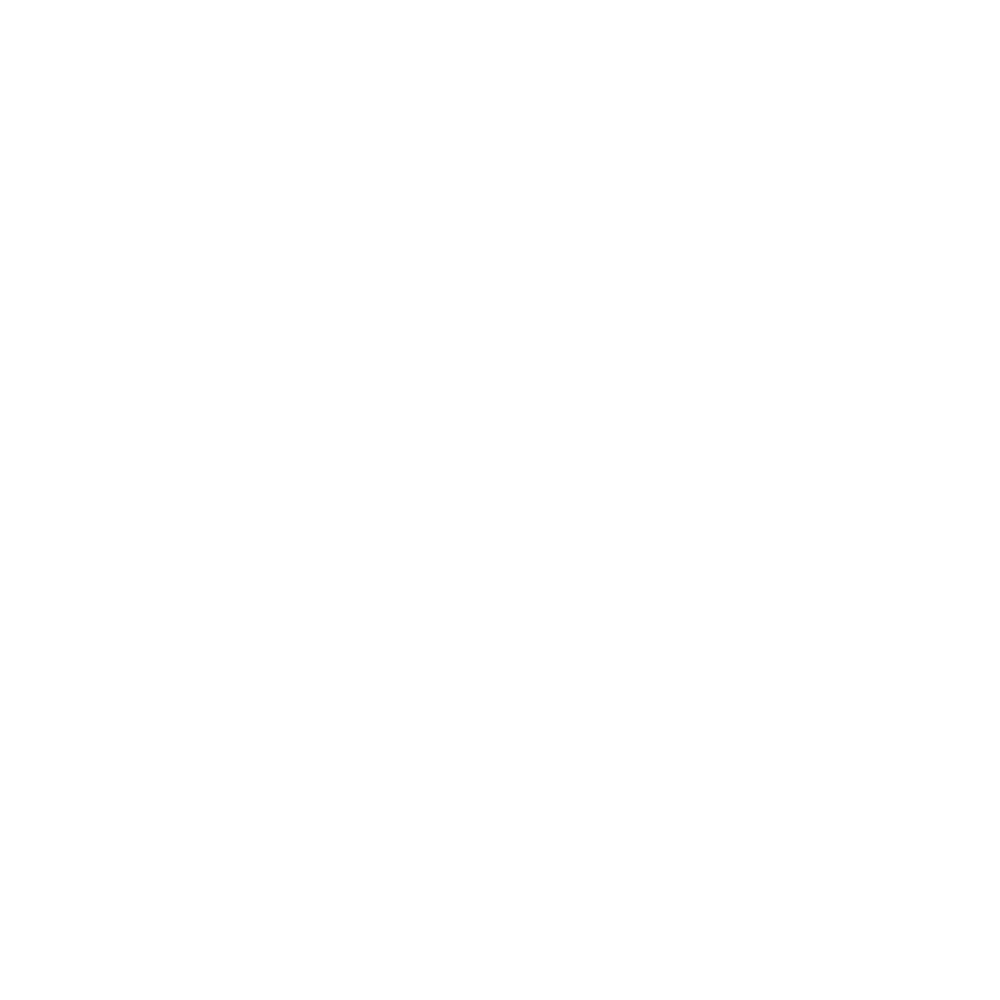
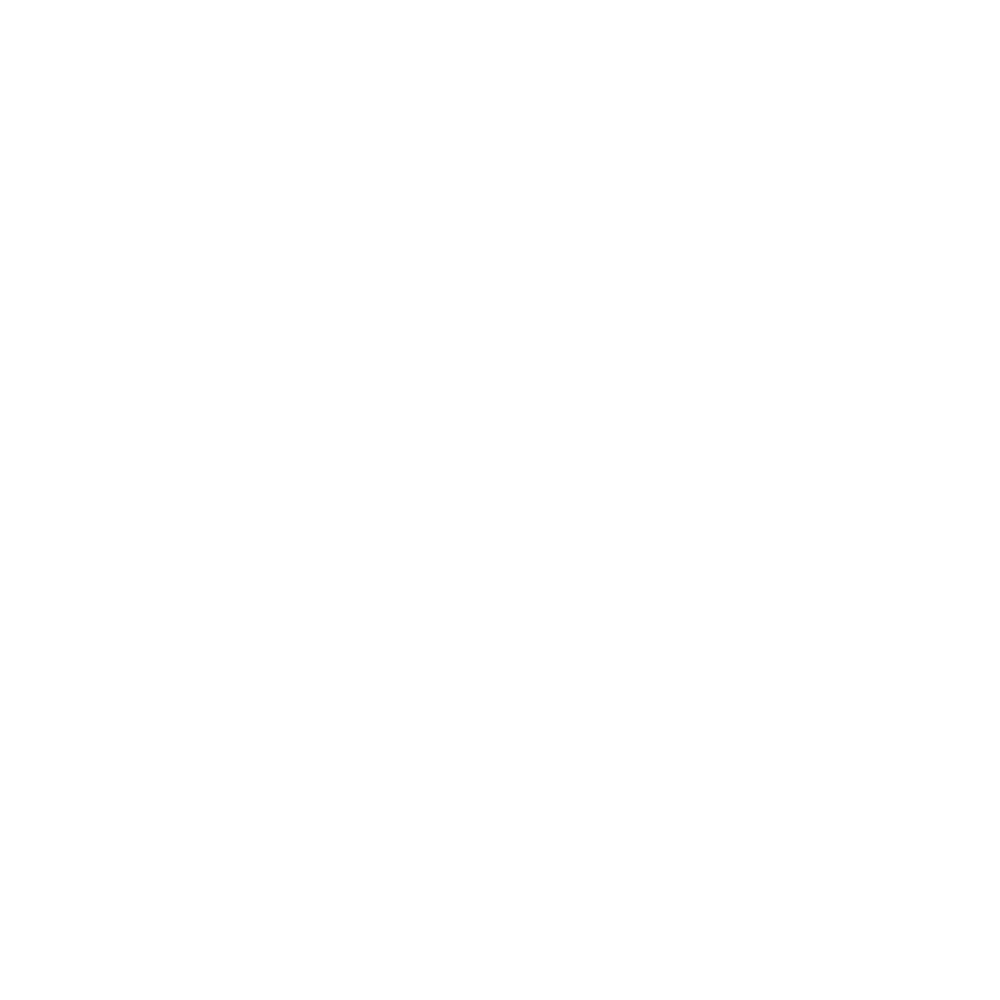
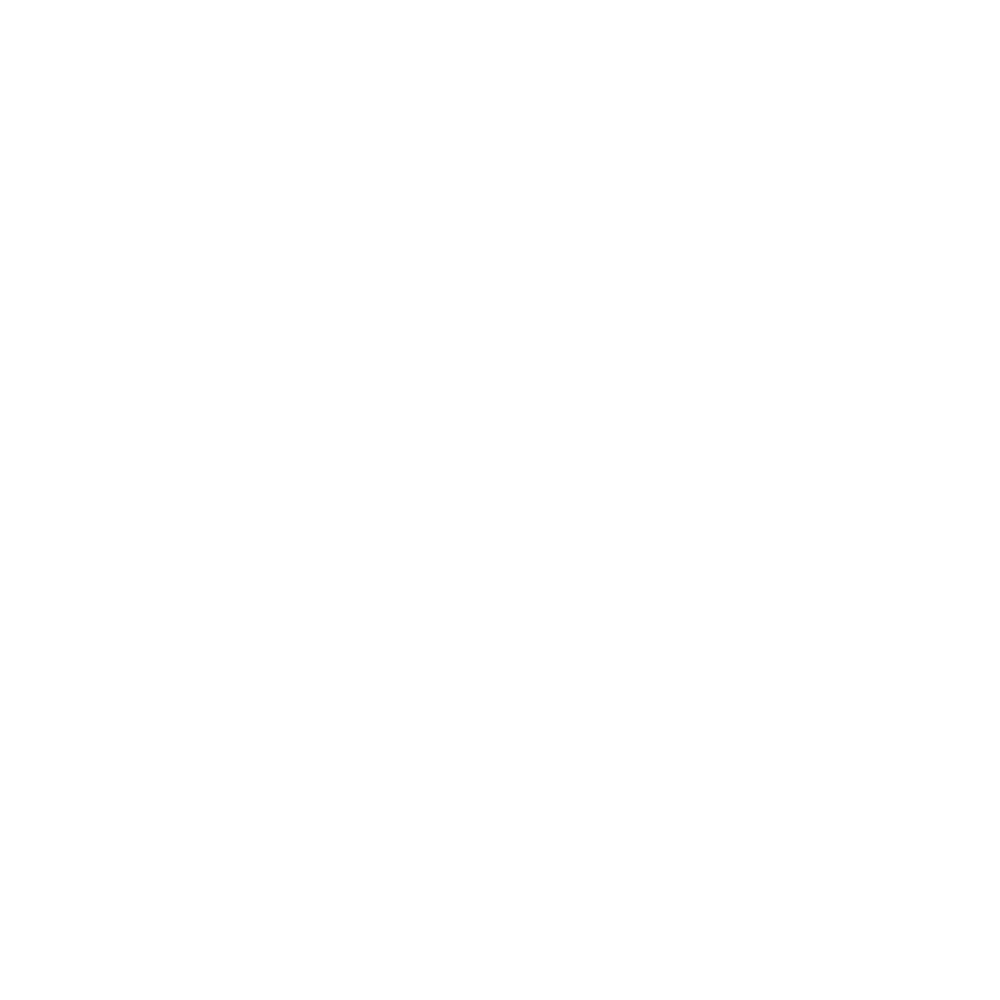
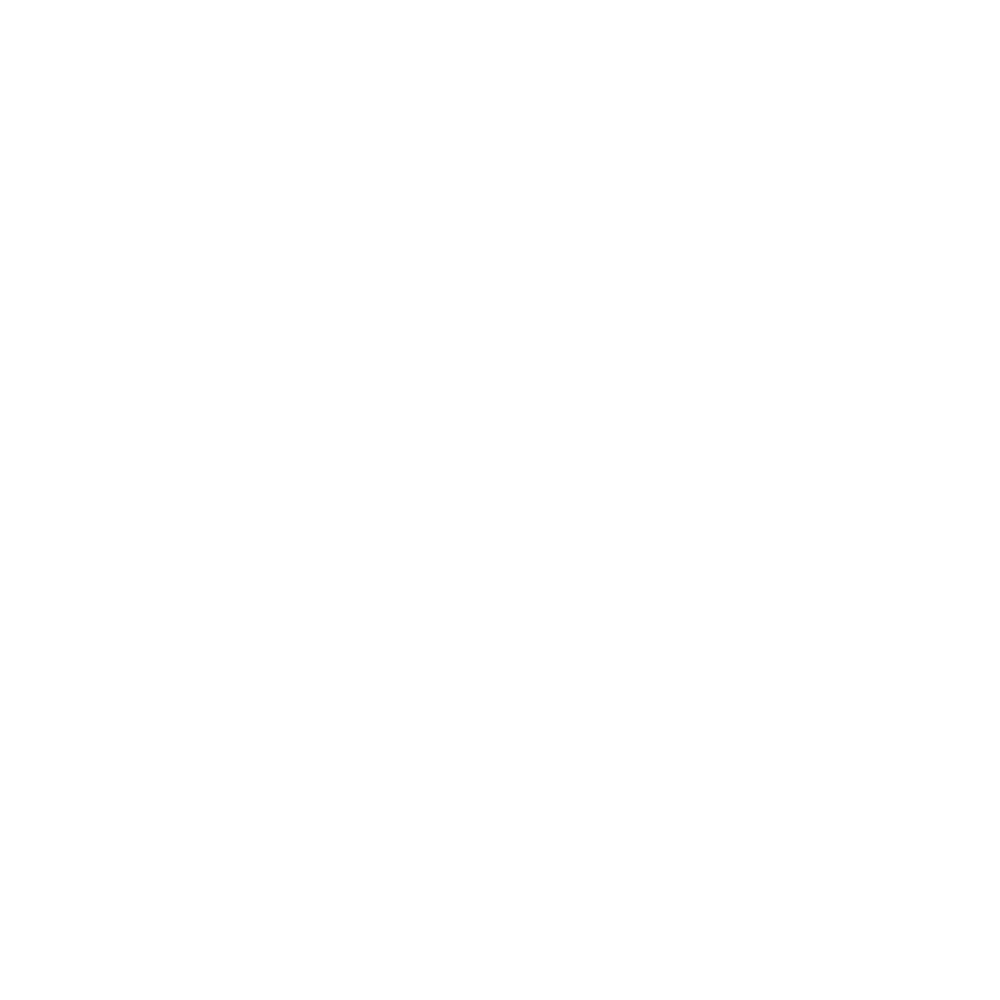
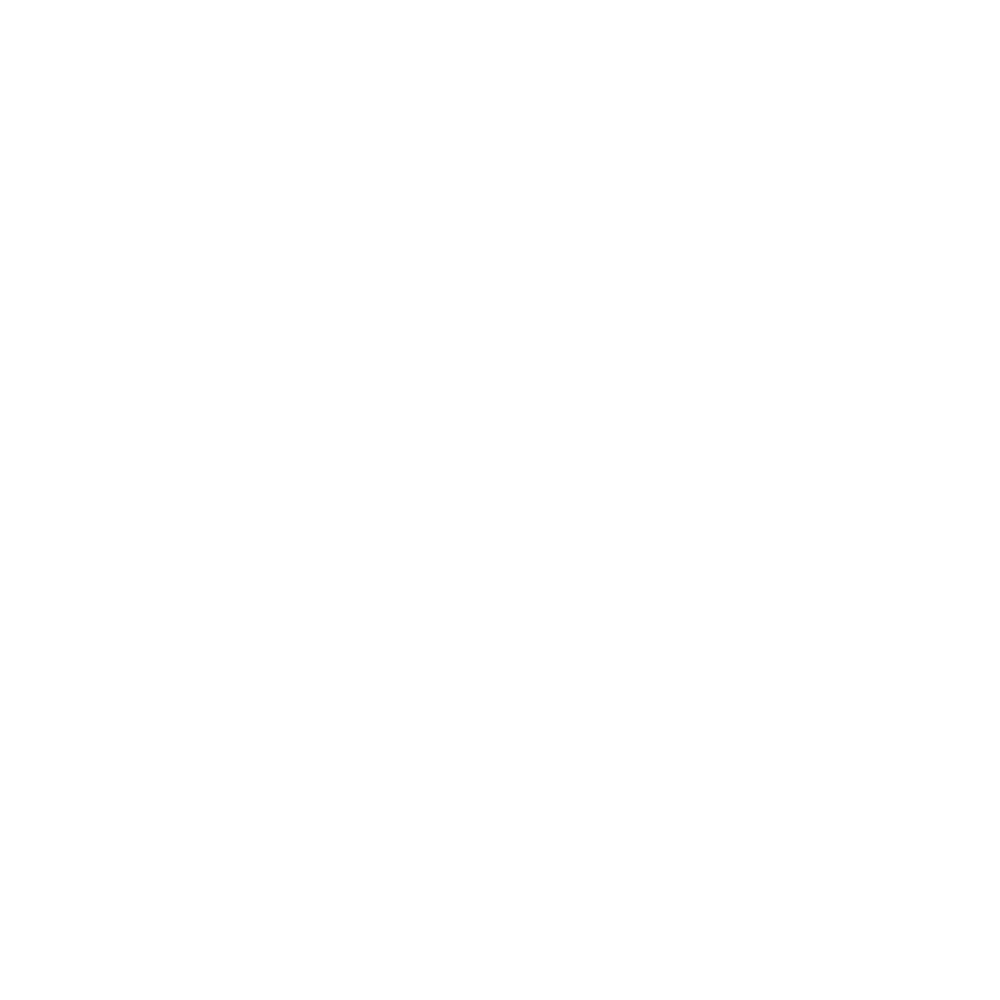
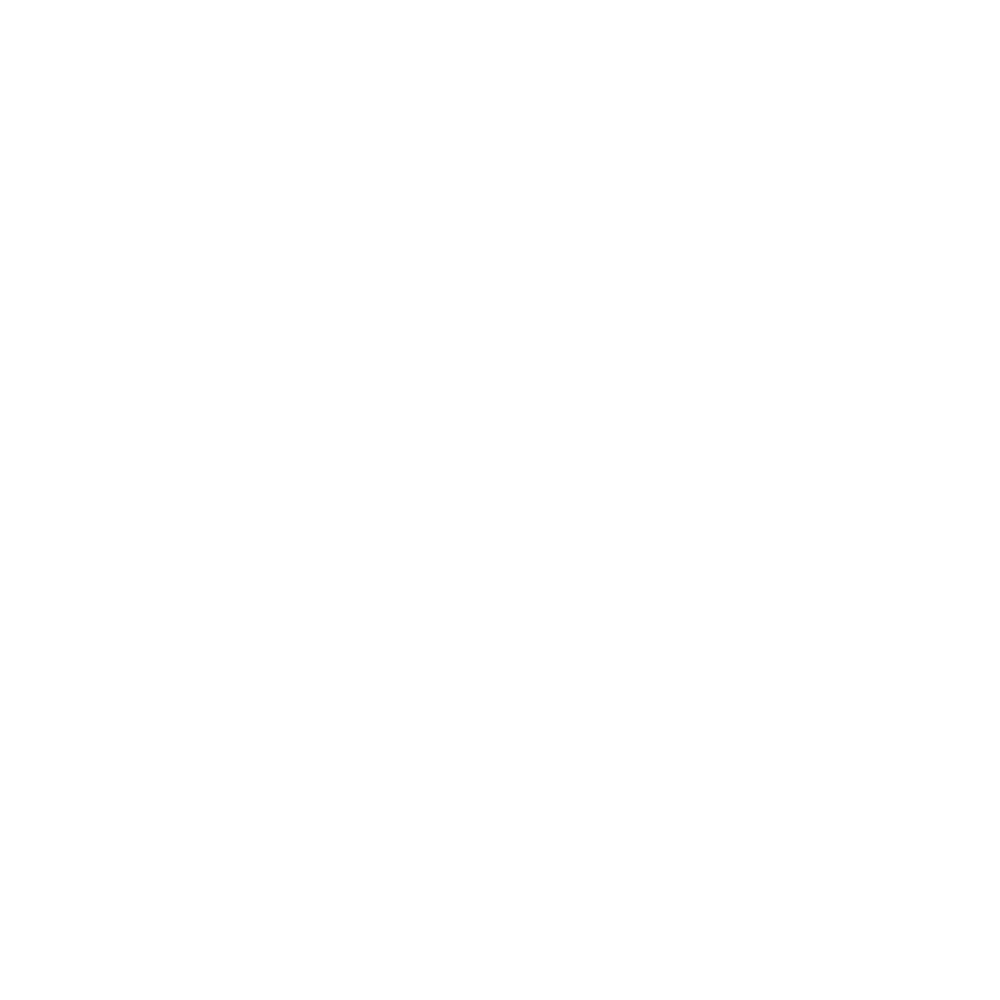
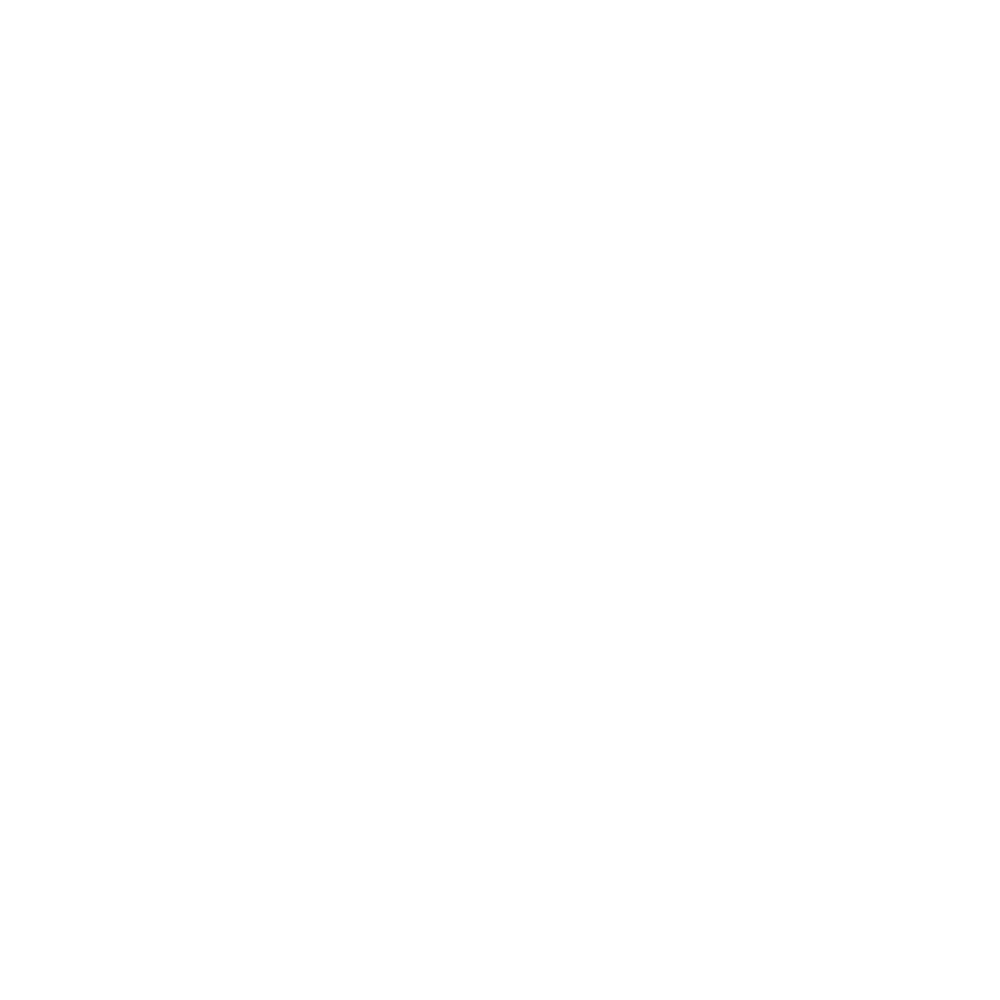
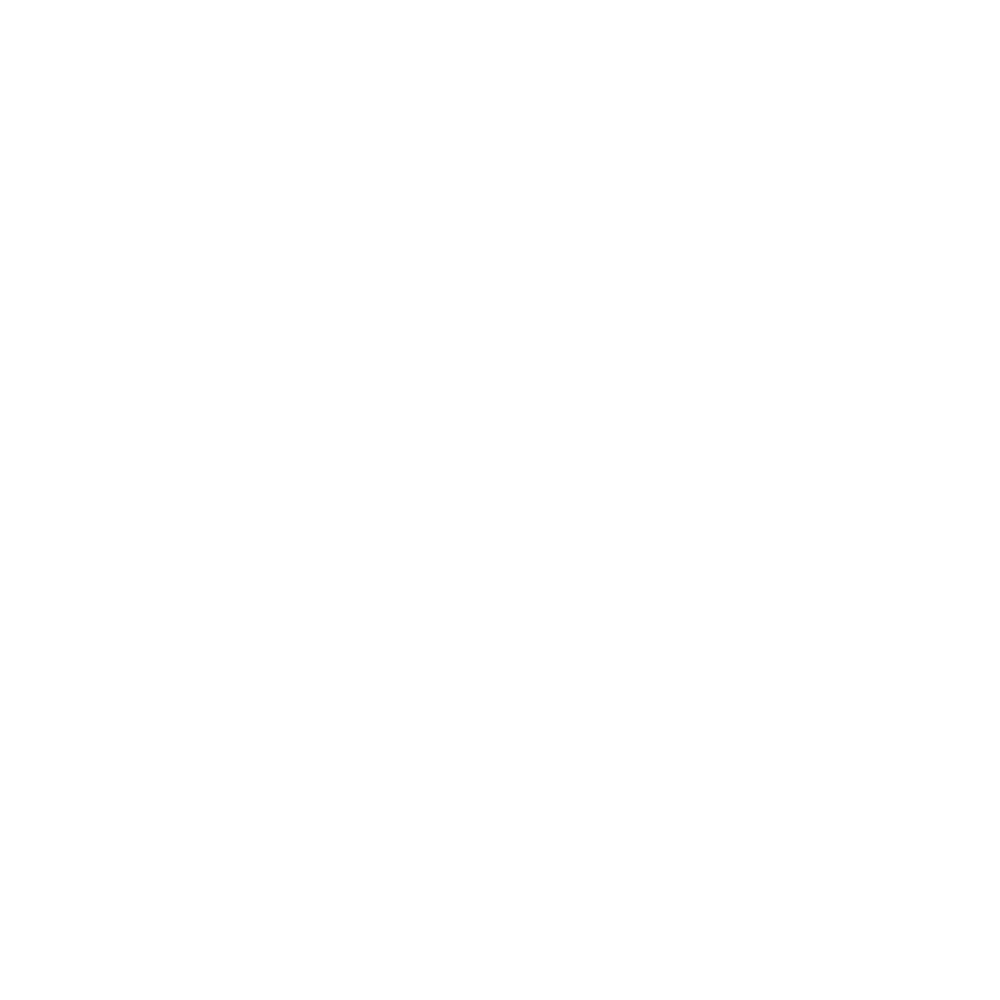
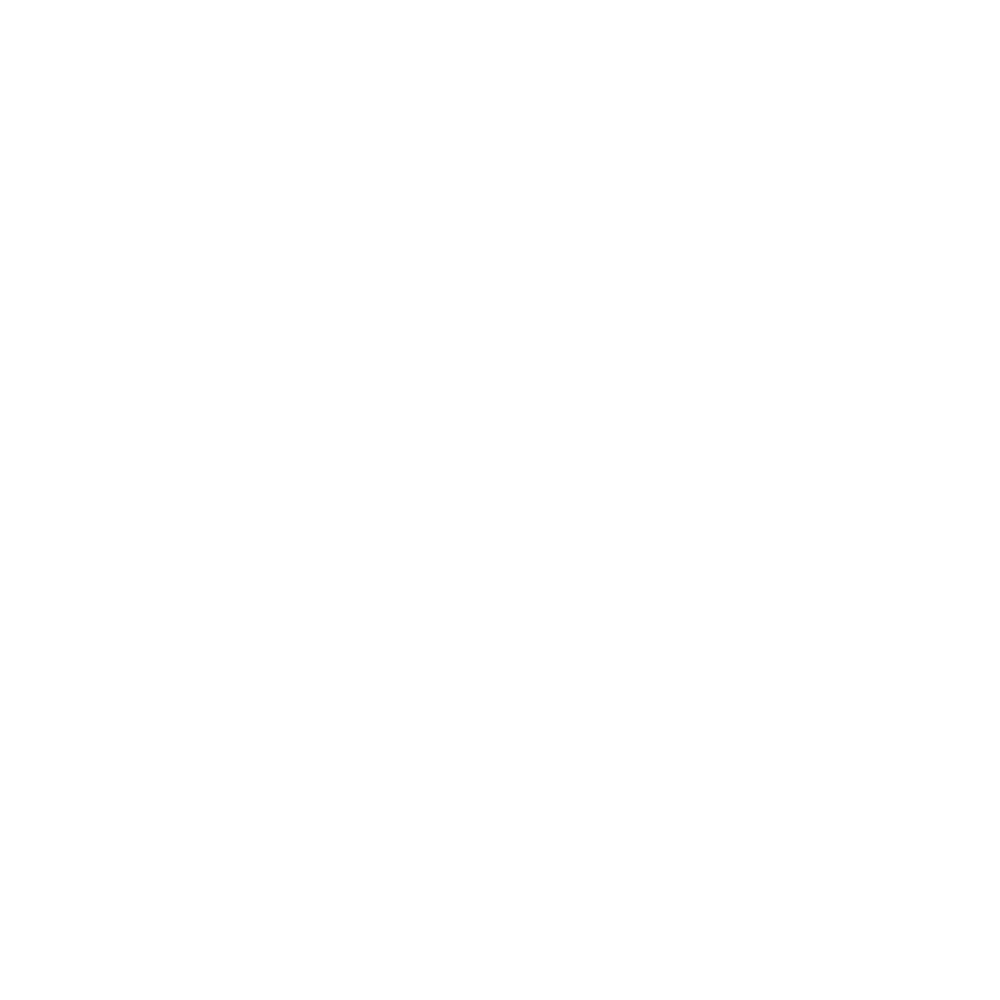
Complex Precision Components
Achieving excellence in complex machining goes beyond having top-of-the-line 5-axis CNC milling machines or cutting-edge CAM and Simulation softwares.
At Tonasco, we excel in fabricating intricate, 3-D features by optimizing a range of machining processes. Some of our most complex components require a combination of Simultaneous 5-axis CNC milling or Multitasking Mill-Turn machines, Wire-EDM, precision grinding with surface treatments or heat treatments.
In addition to complex features, we excel in producing parts with High Surface Finishing, catering to specialized needs such as black matte finishing for optomechanical components and optimal seal surface finishing for vacuum chambers.
Investing in leading Hypermill CAM and Simulation softwares allows us to program intricate milling strategies, while simulation software enables us to test our programs on digital twins of milling centers, eliminating errors and preventing costly mistakes.
Our proficiency in complex milling and high surface finishing is honed through continuous challenges and testing of cutting strategies, coupled with relentless improvement of cutting parameters. With extensive knowledge and experience in handling challenging materials such as titanium, hardened carbides, and special plastics, we are well-equipped to tackle the most demanding machining projects.
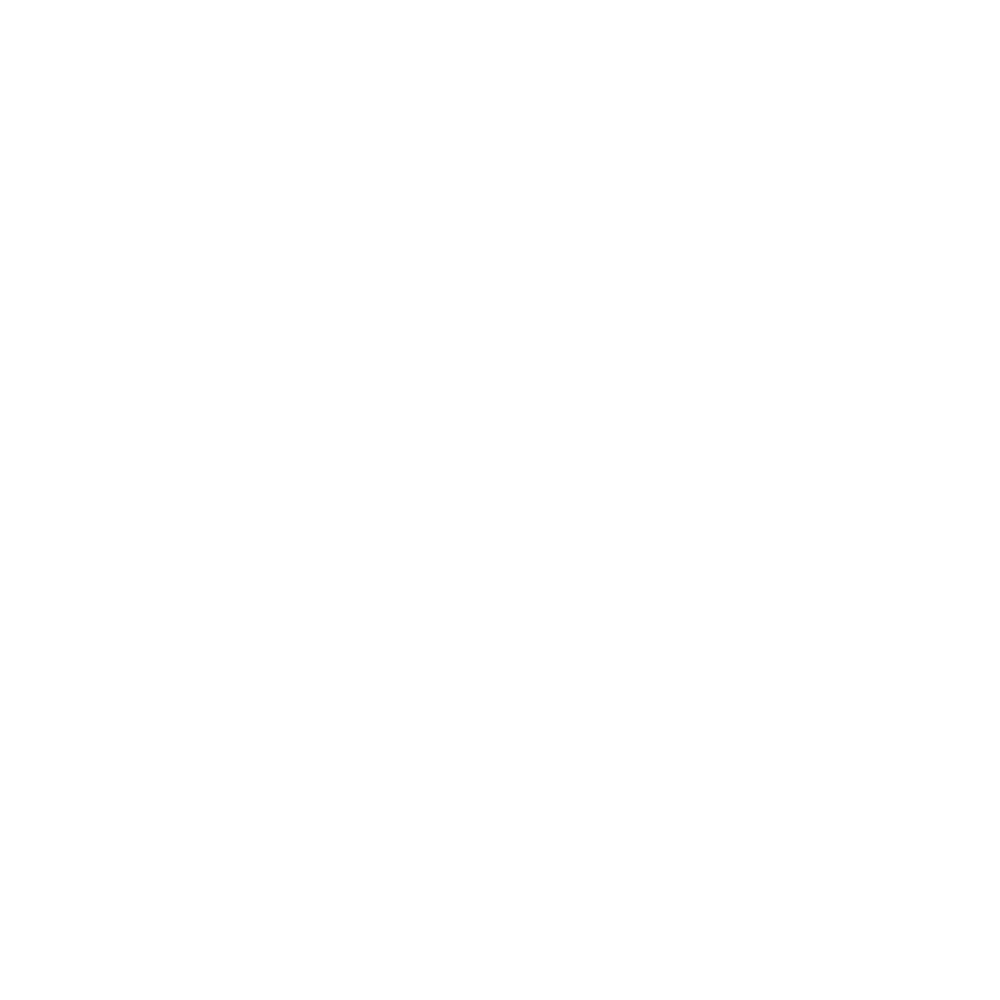
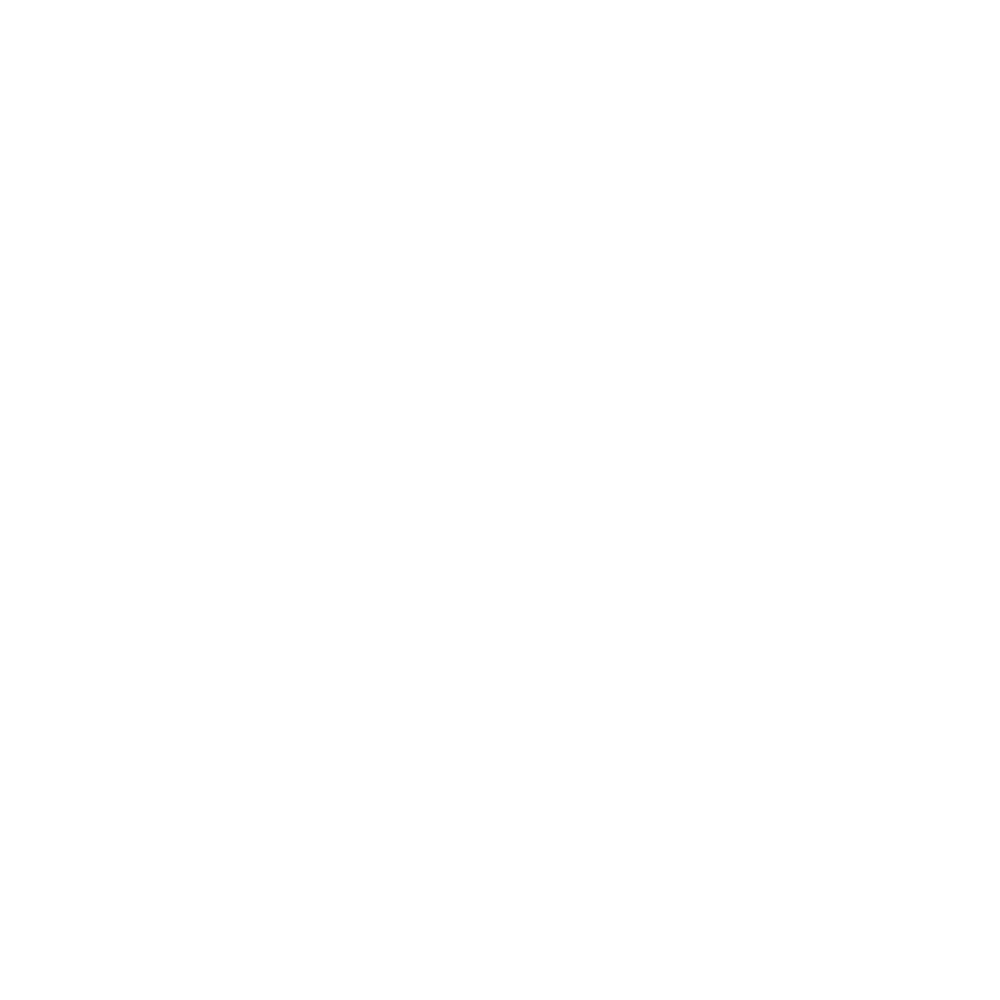
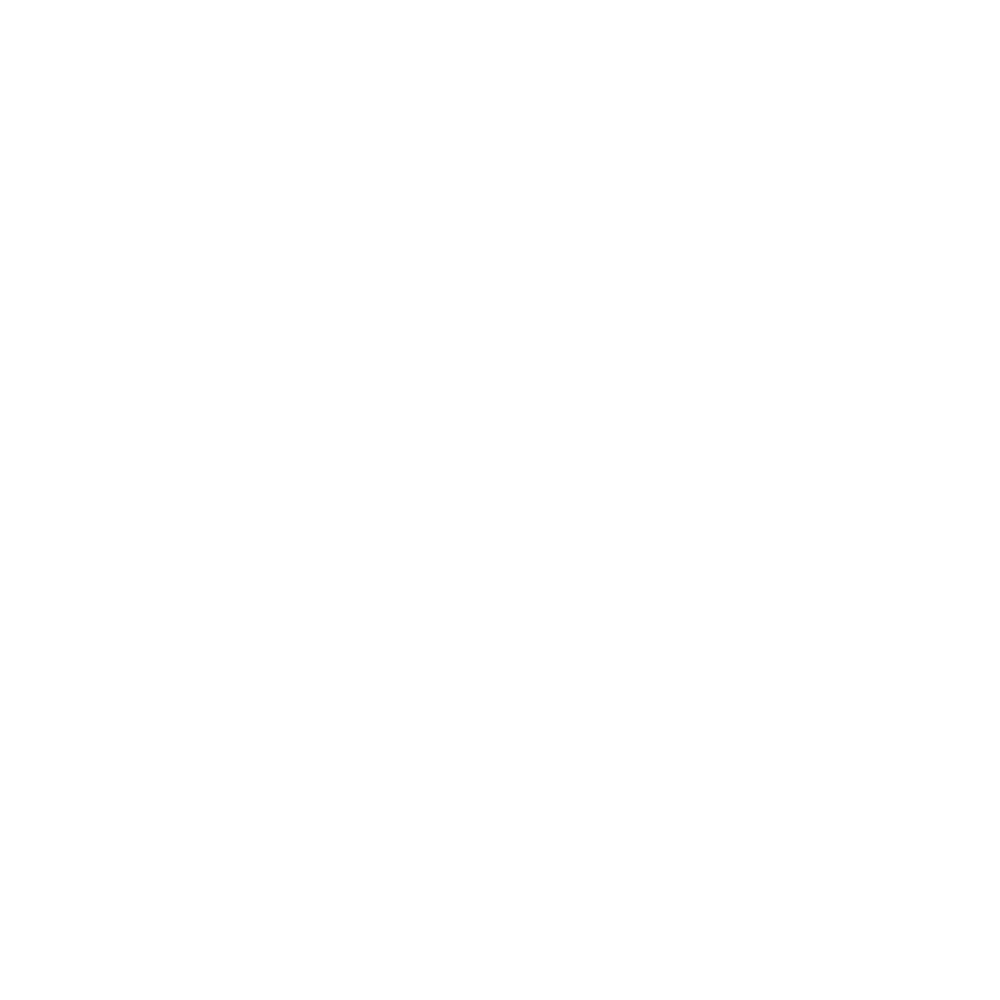
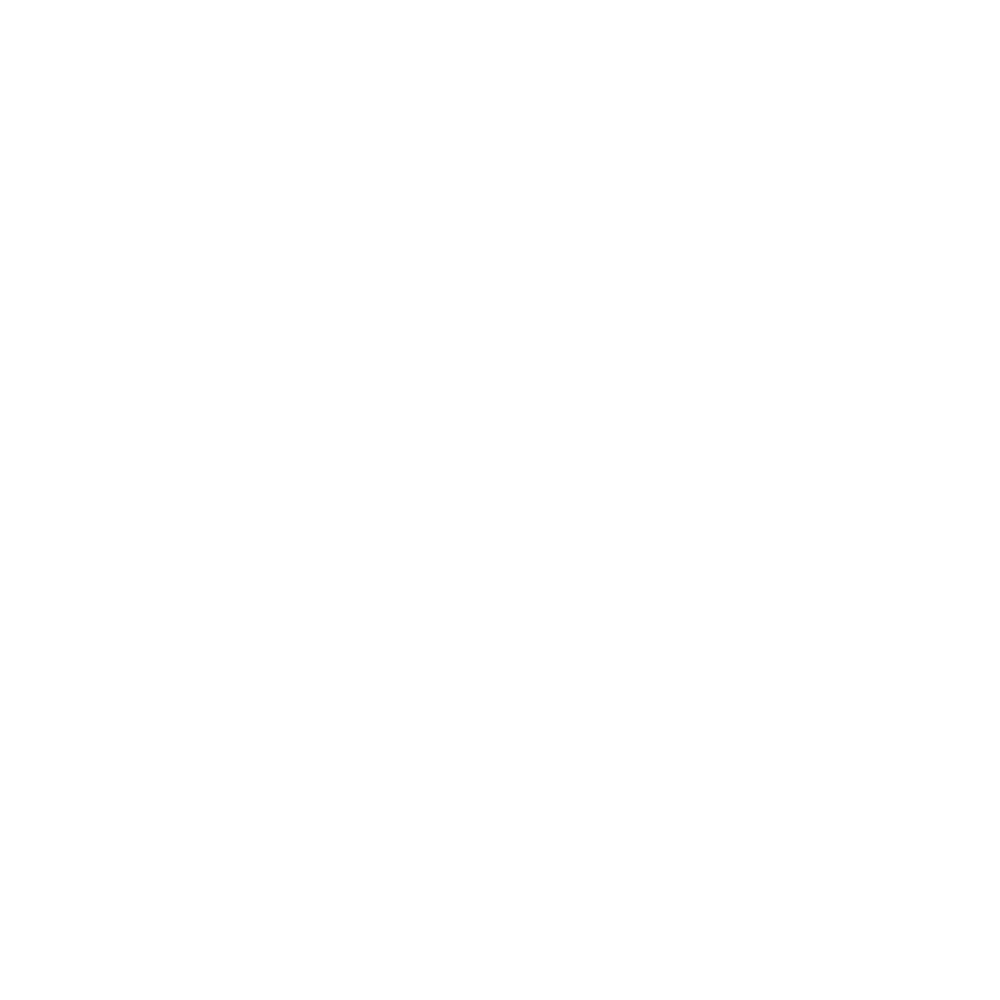
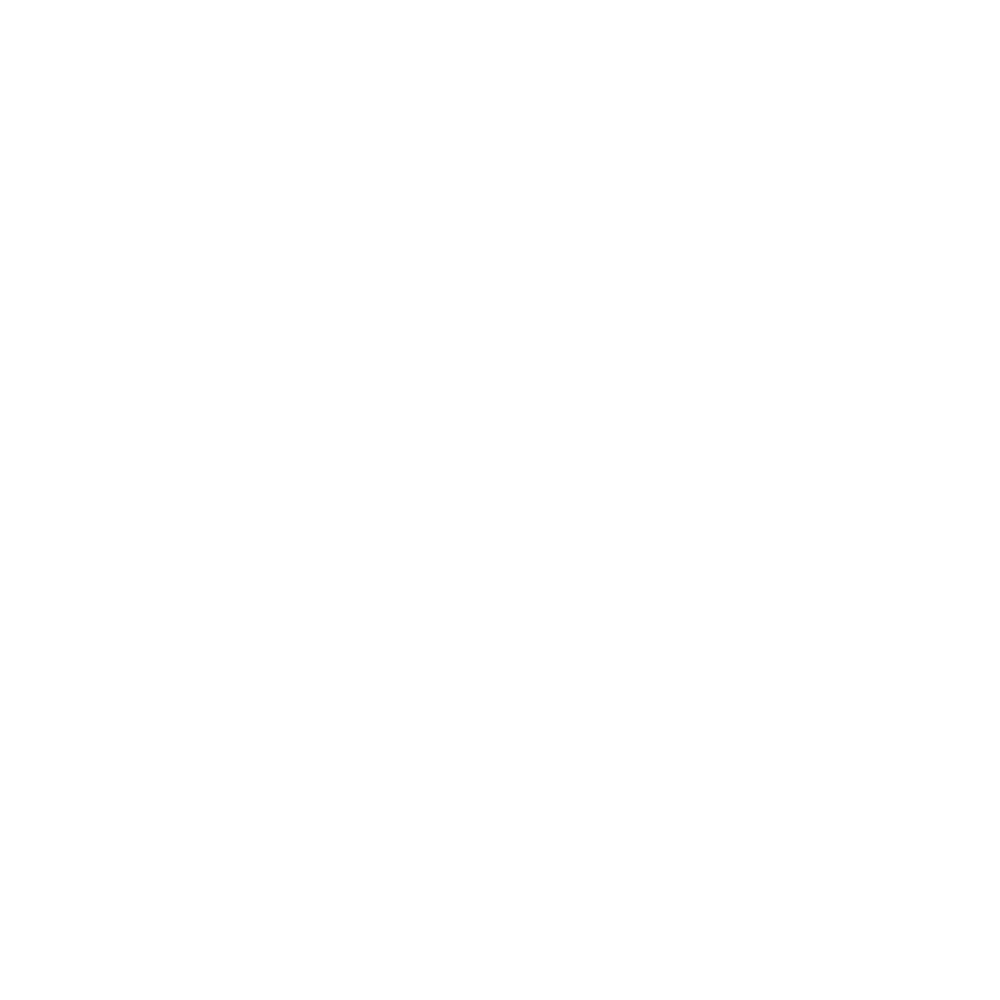
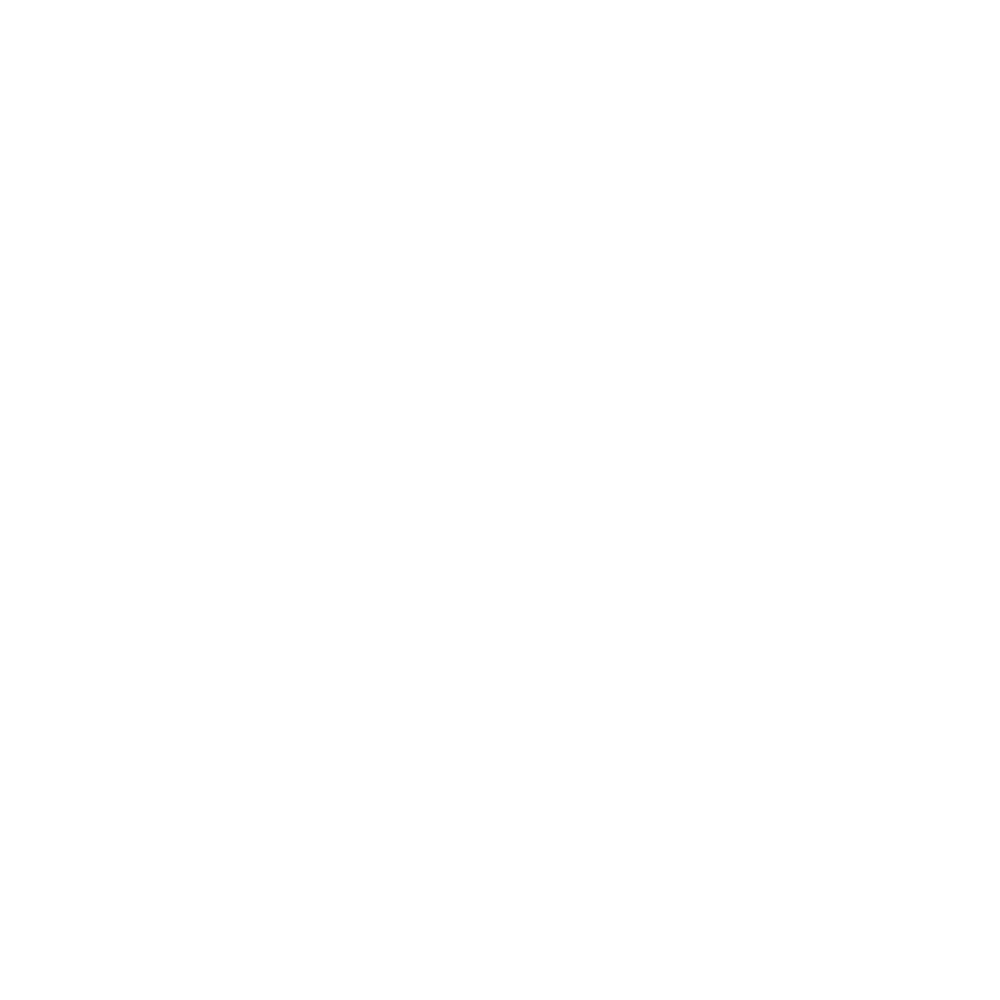
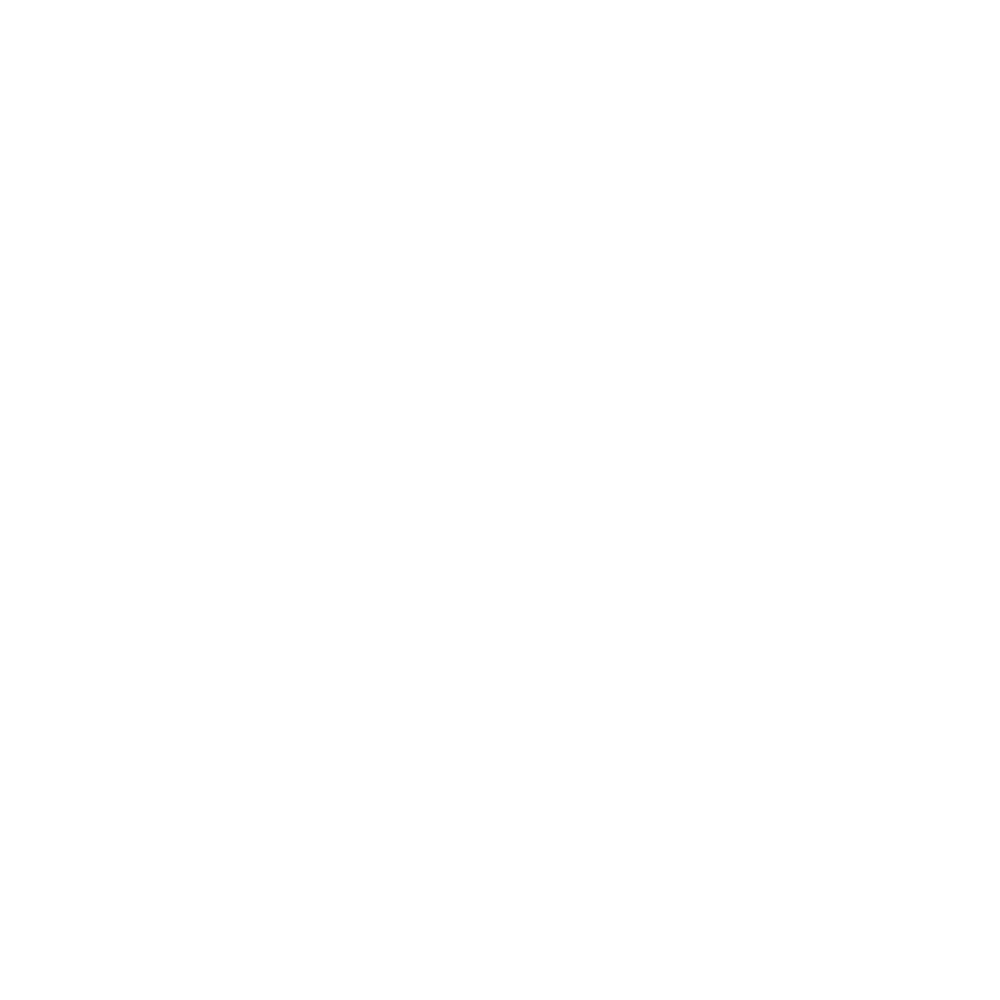
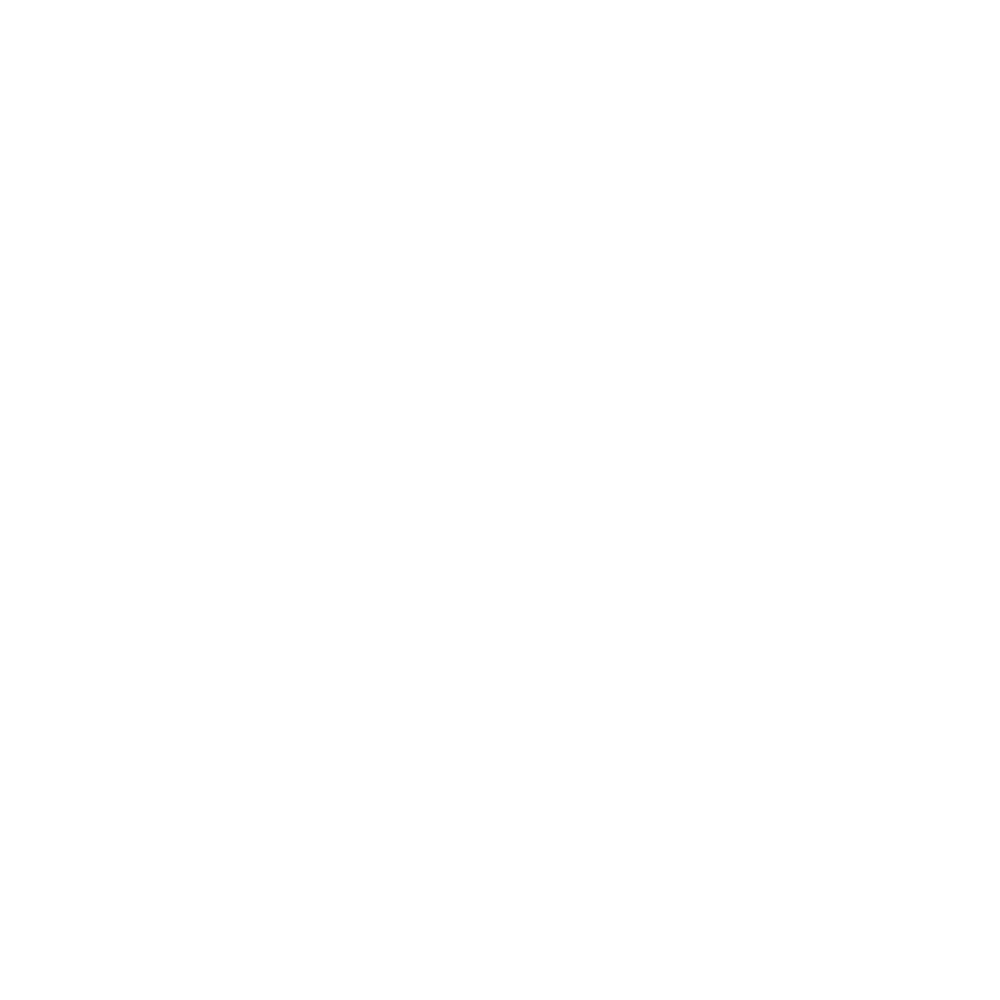
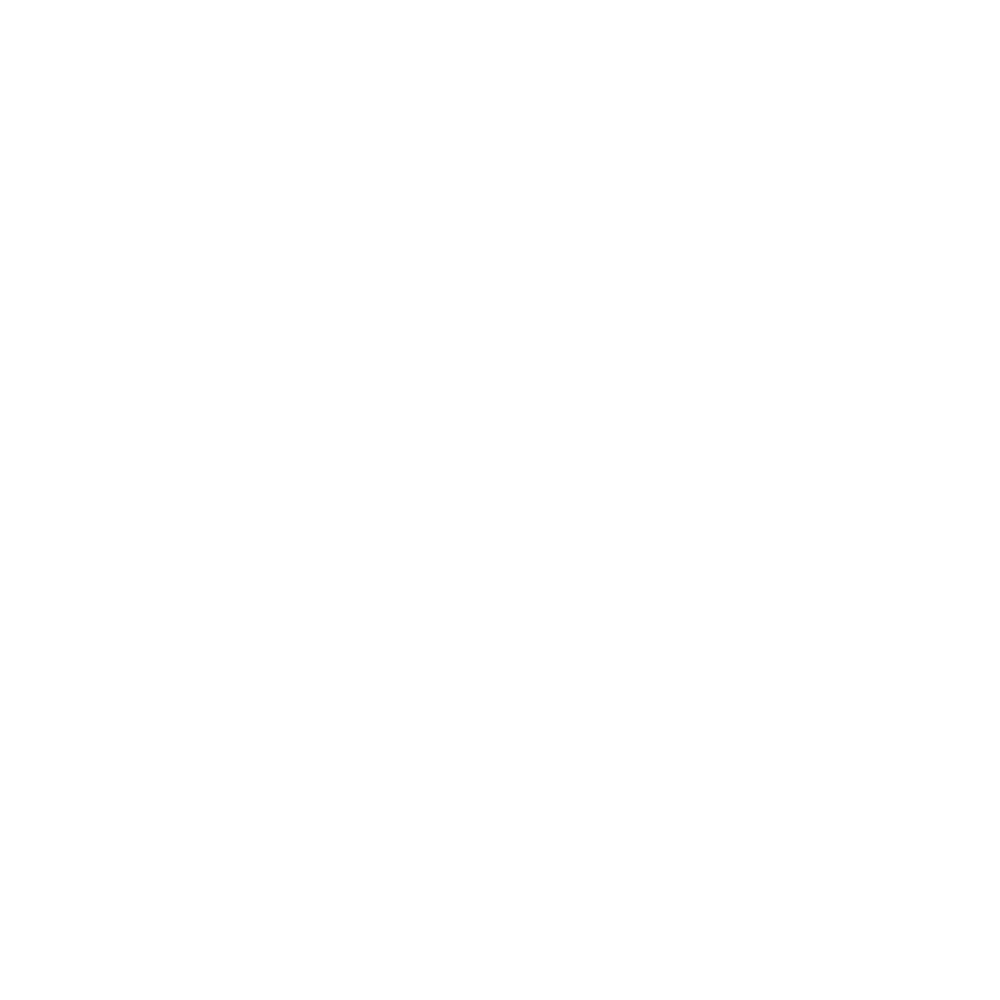
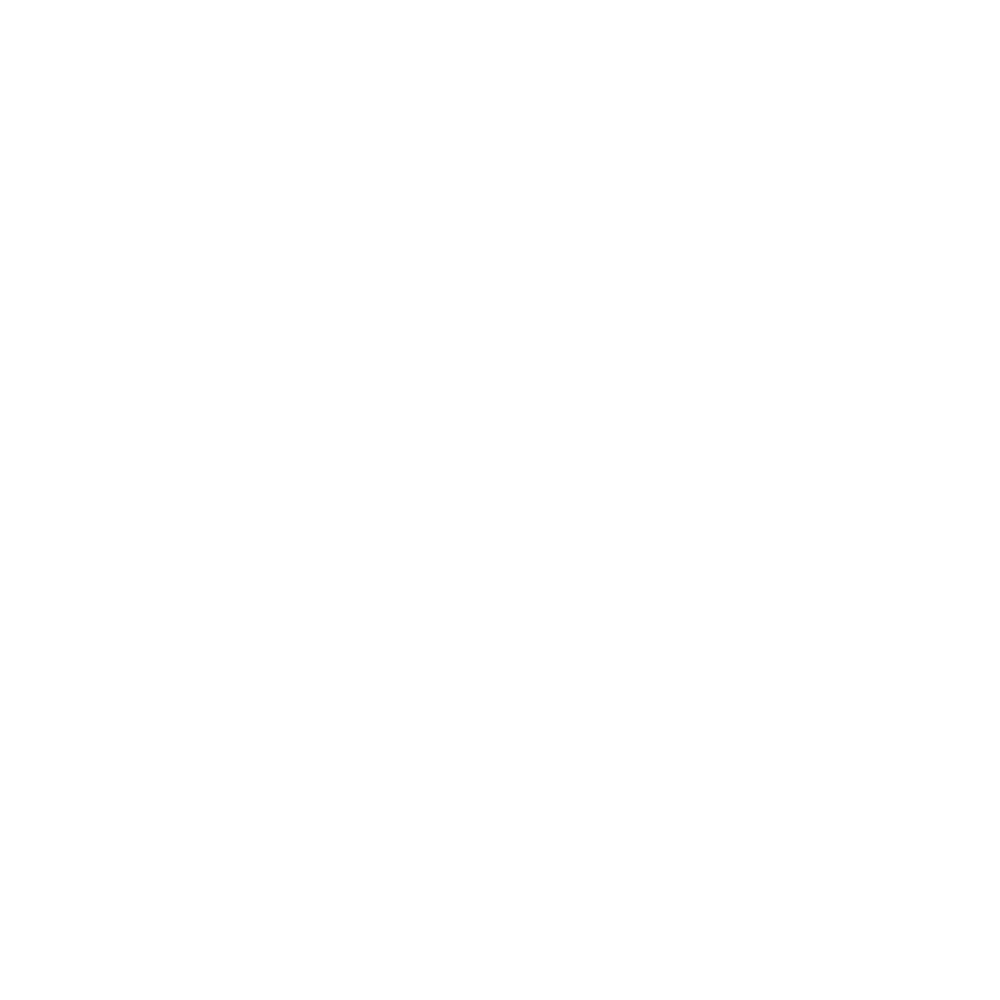
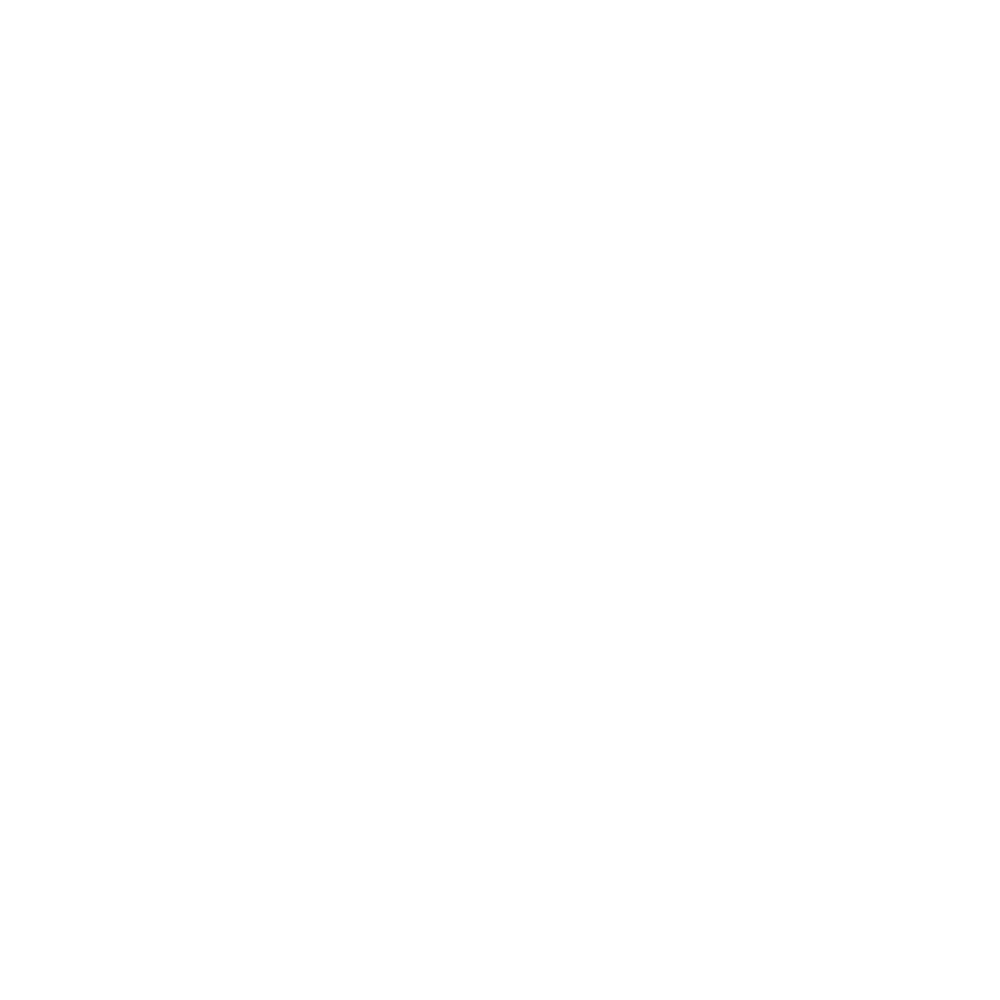
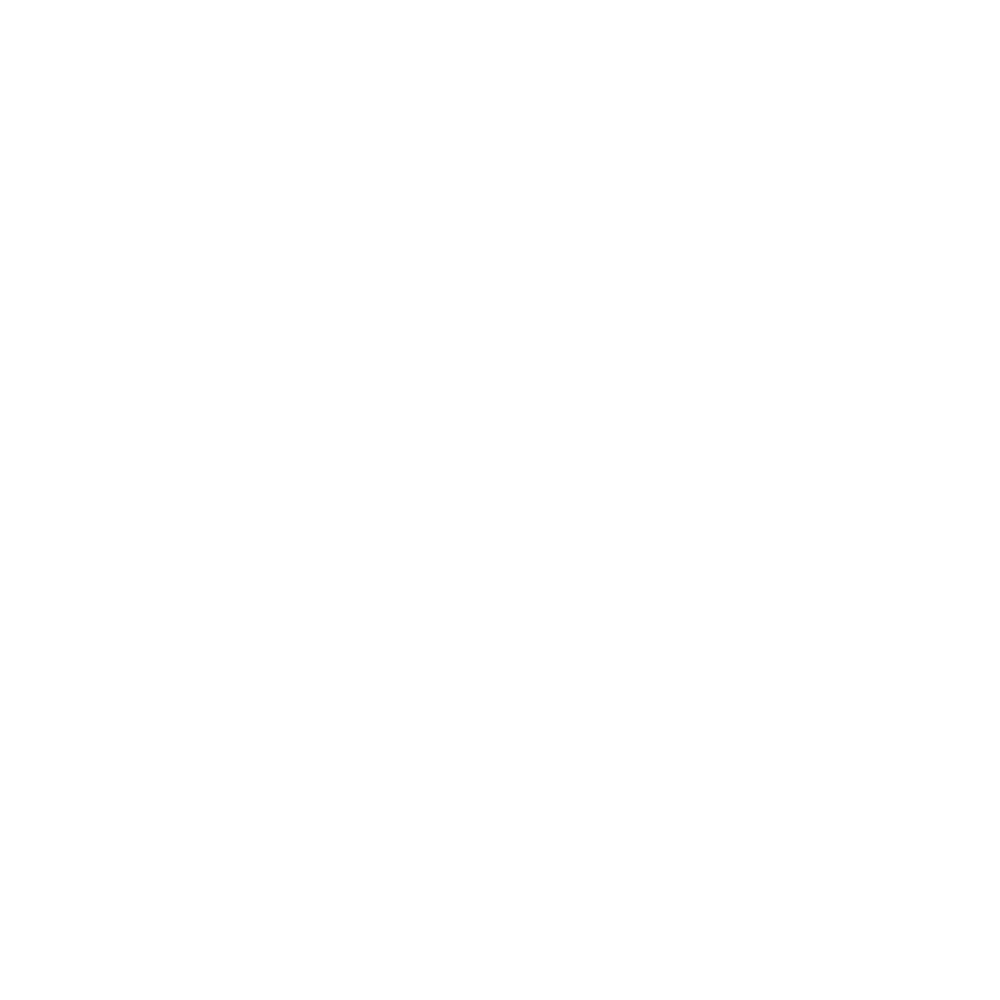
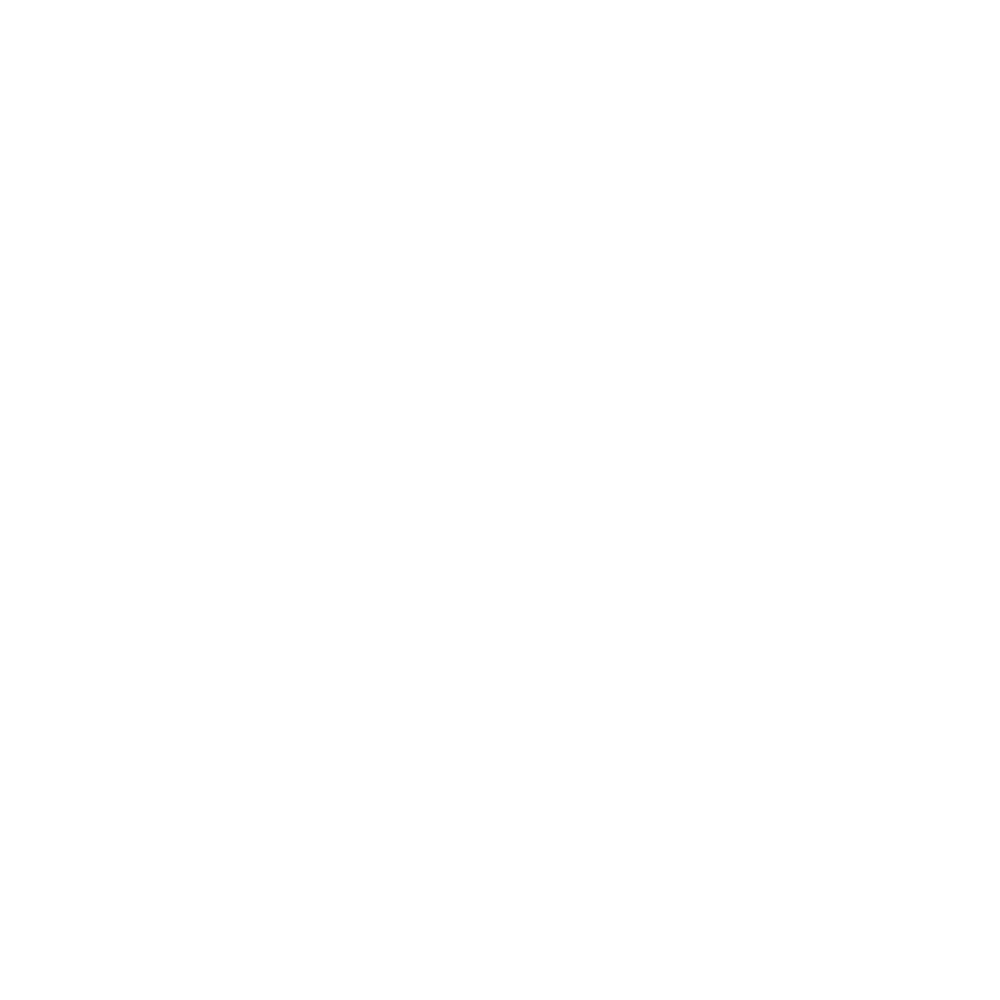
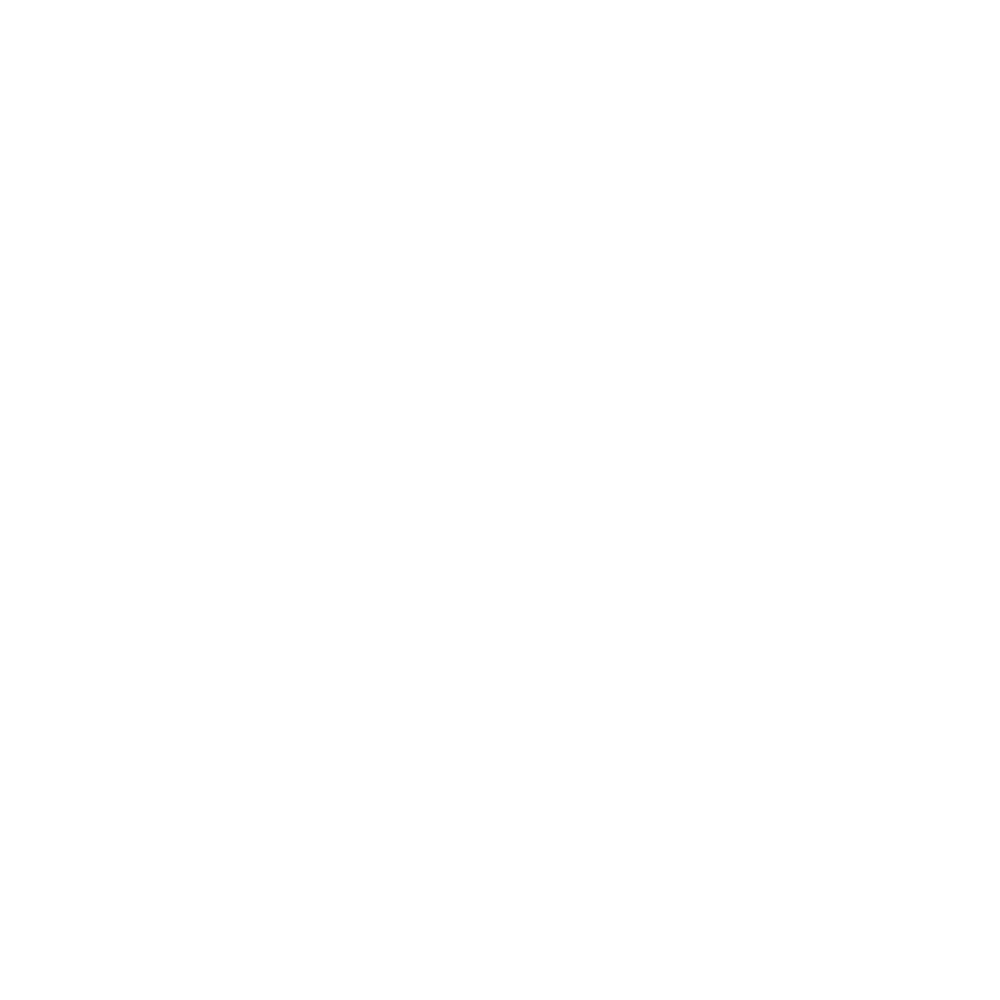
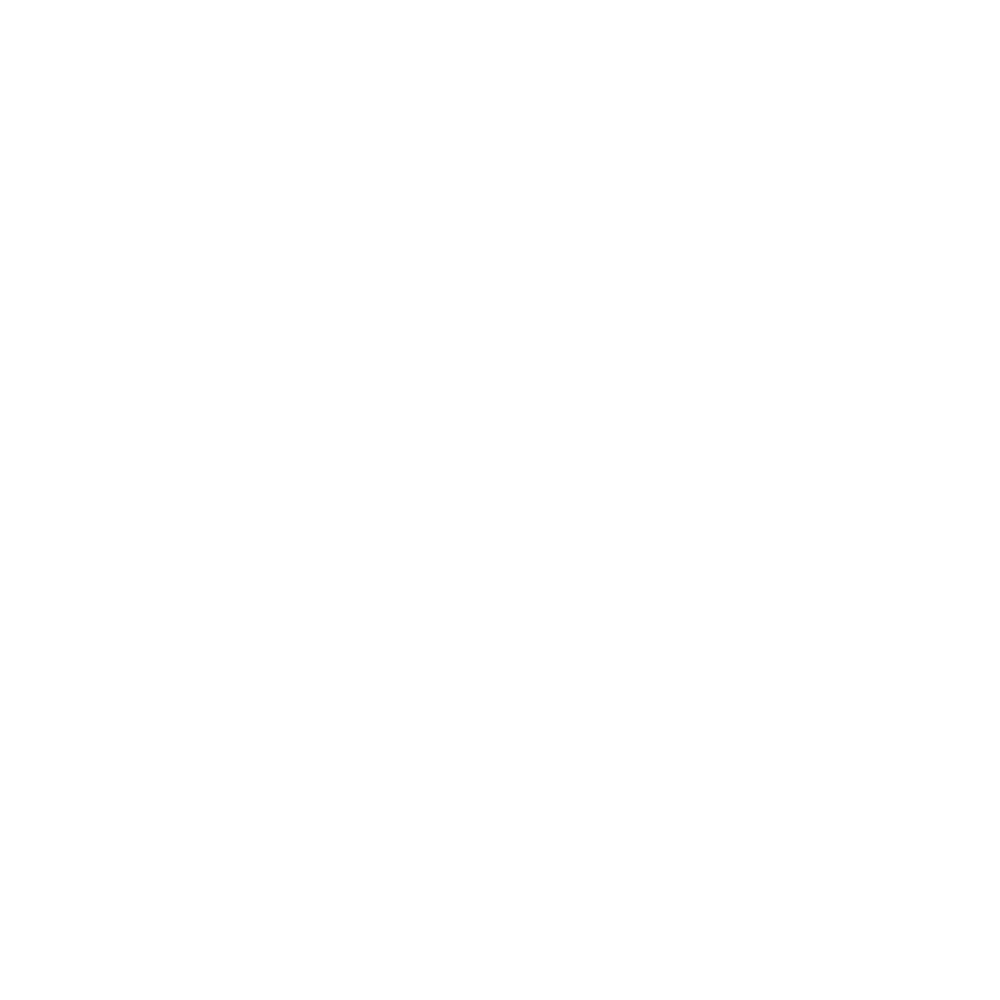
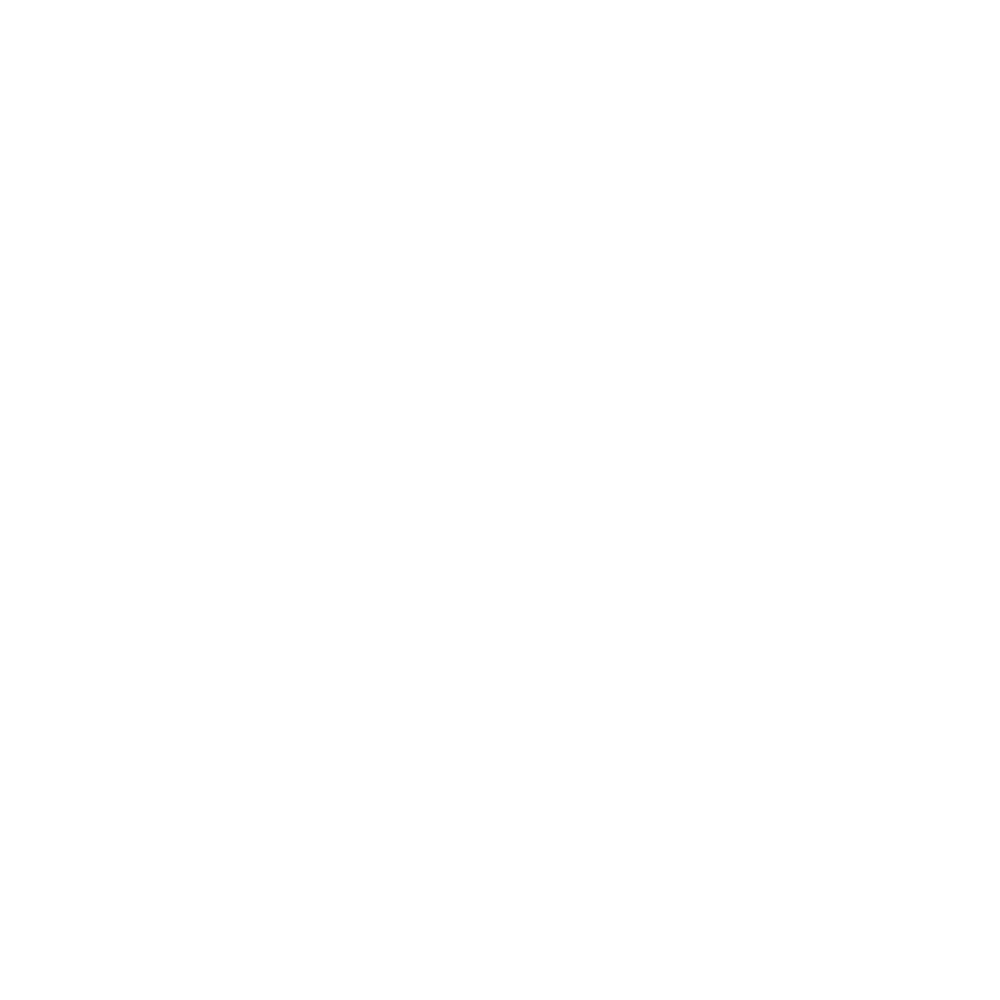
Cleanroom Precision Components
At our facilities, we specialize in producing clean components that meet ASML Grade 2 cleanliness standards. Our expertise extends to clean production techniques tailored to the Semiconductor, Optical, Medical, and Diagnostics industries. Equipped with state-of-the-art facilities, including 5-stage ultrasonic cleaning facilities and ISO-6 certified laminar flow benches, we ensure meticulous cleanliness at every stage of production.
Our commitment to quality is evidenced by our verification and qualification for Ultra-High Vacuum (UHV) components production. Rigorous contamination controls are implemented throughout our production protocols, from material selection to surface finishing, ultrasonic cleaning, vacuum baking, and double vacuum packing for shipment to customers.
Environmental sustainability is at the core of our operations. We prioritize clean and green cleaning methods, seeking the best water-based, eco-friendly detergents that leave no harmful residue on components or in wastewater. Our dedication to sustainability extends to removing stubborn contaminants like siloxane residues, which could jeopardize critical applications such as laser systems in vacuum chambers.
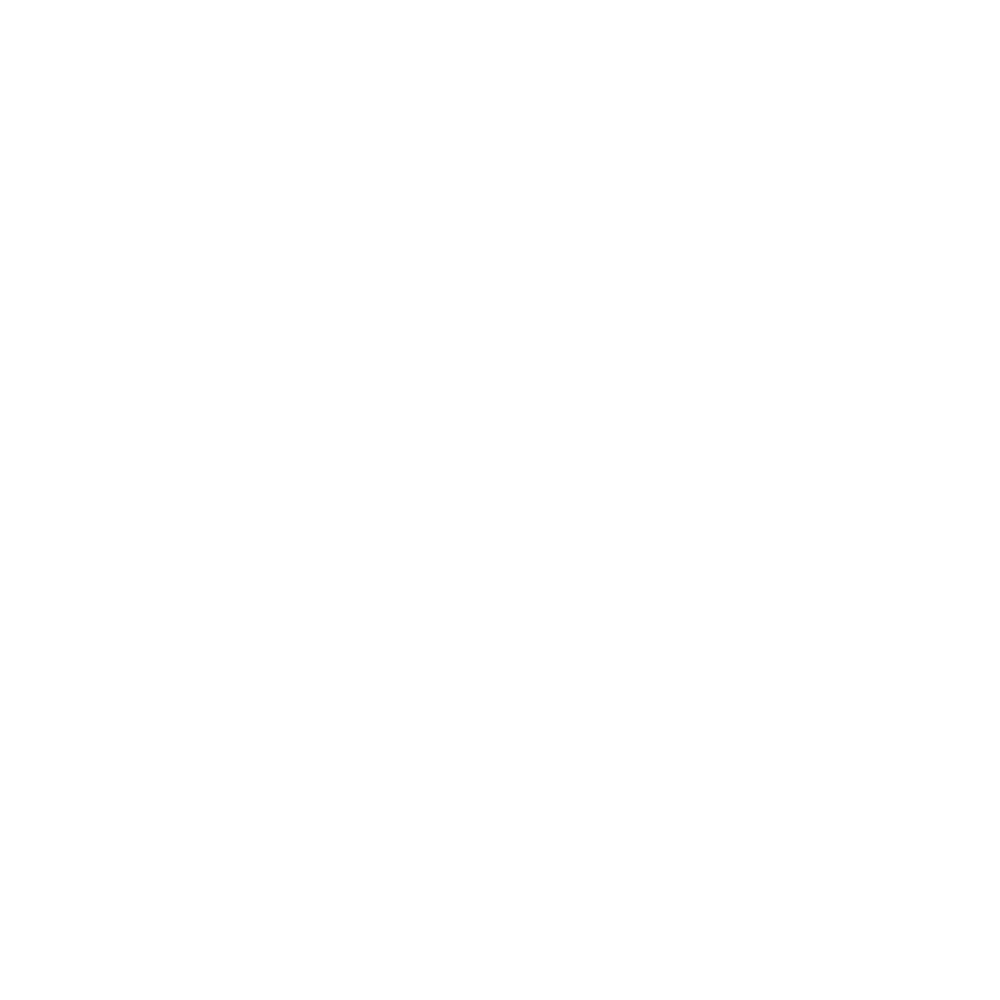
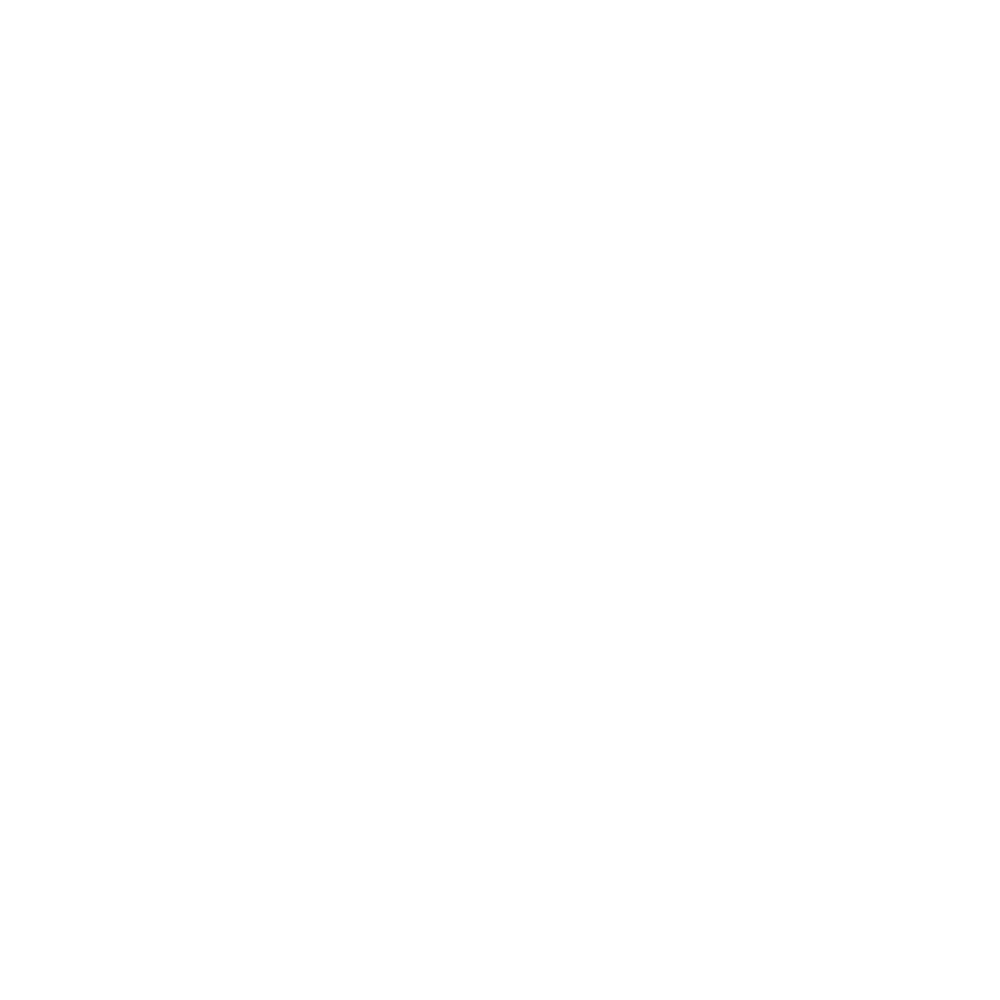
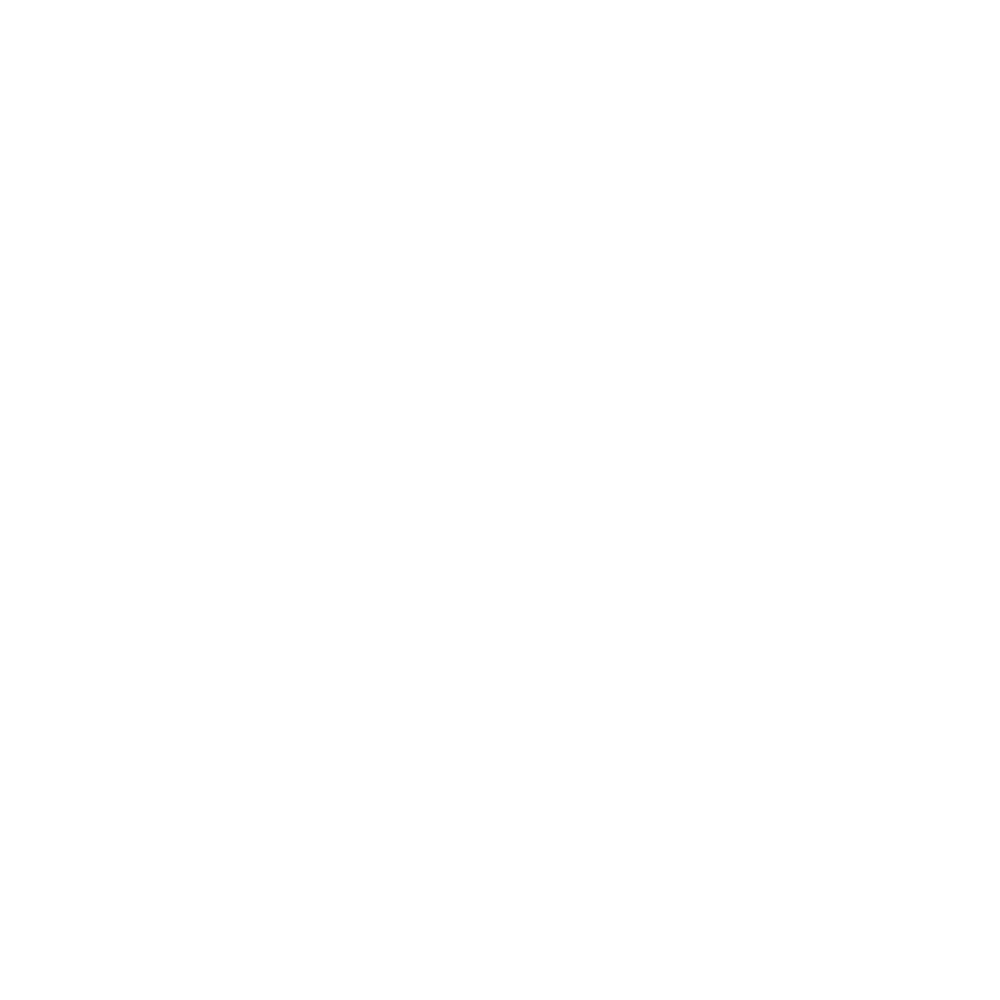
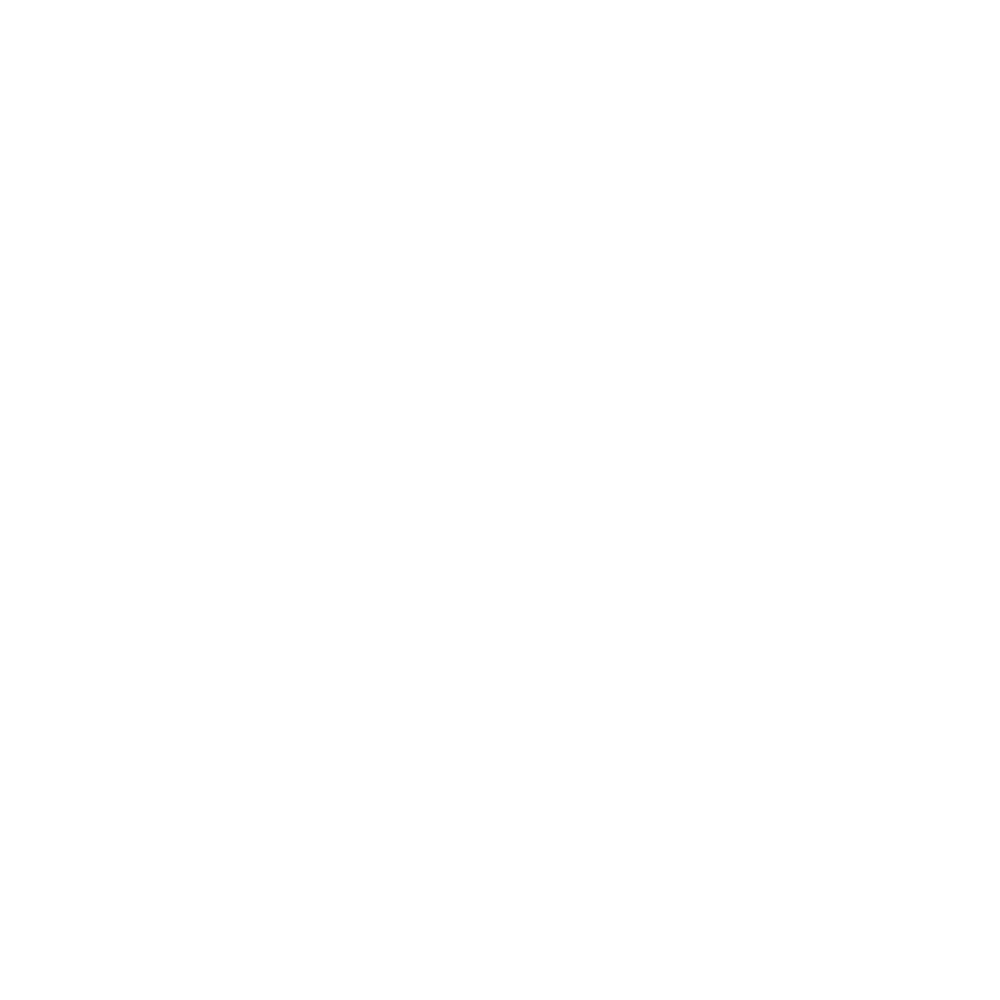
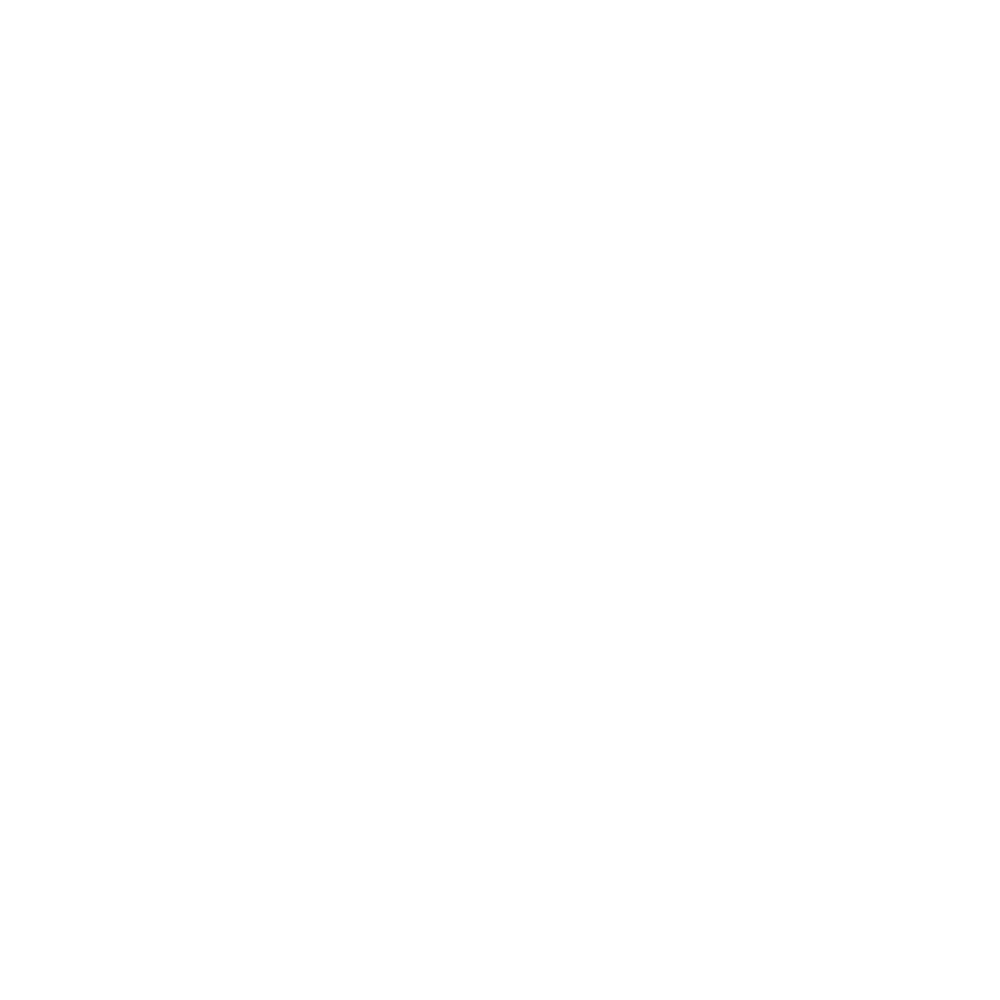
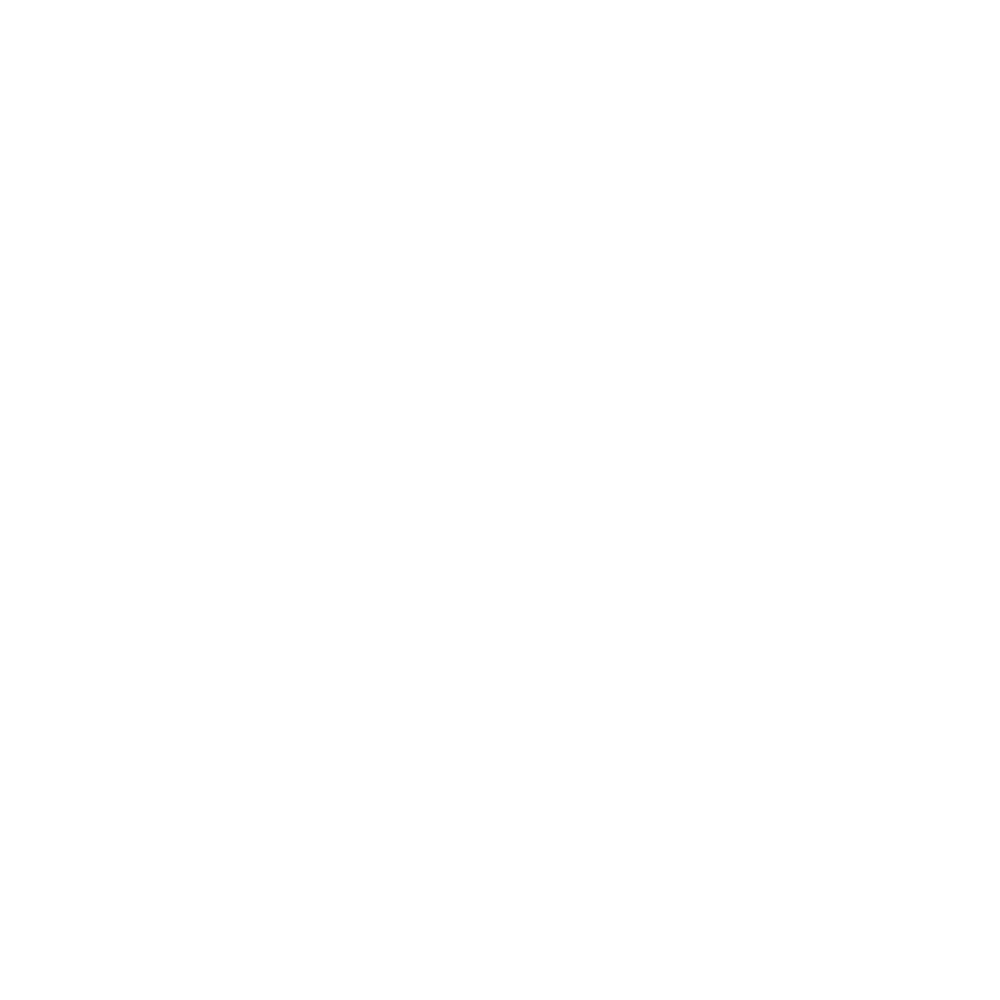
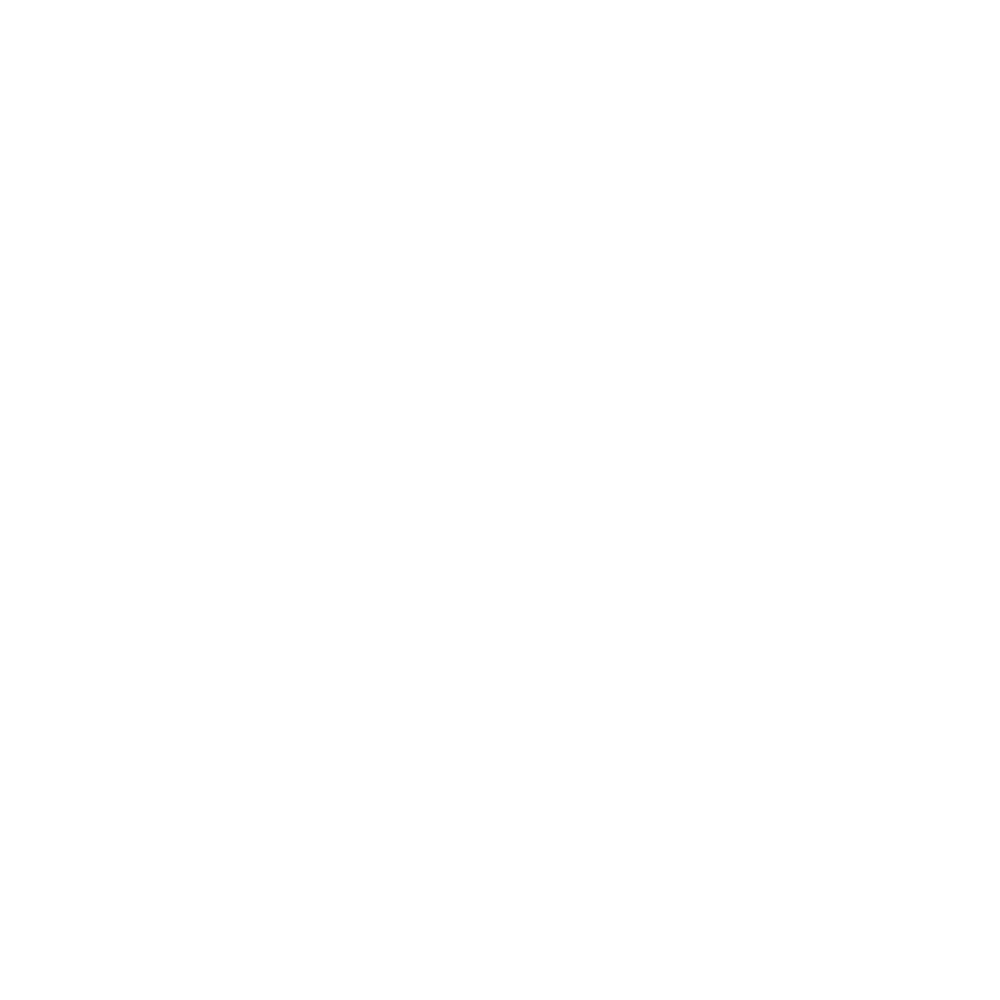
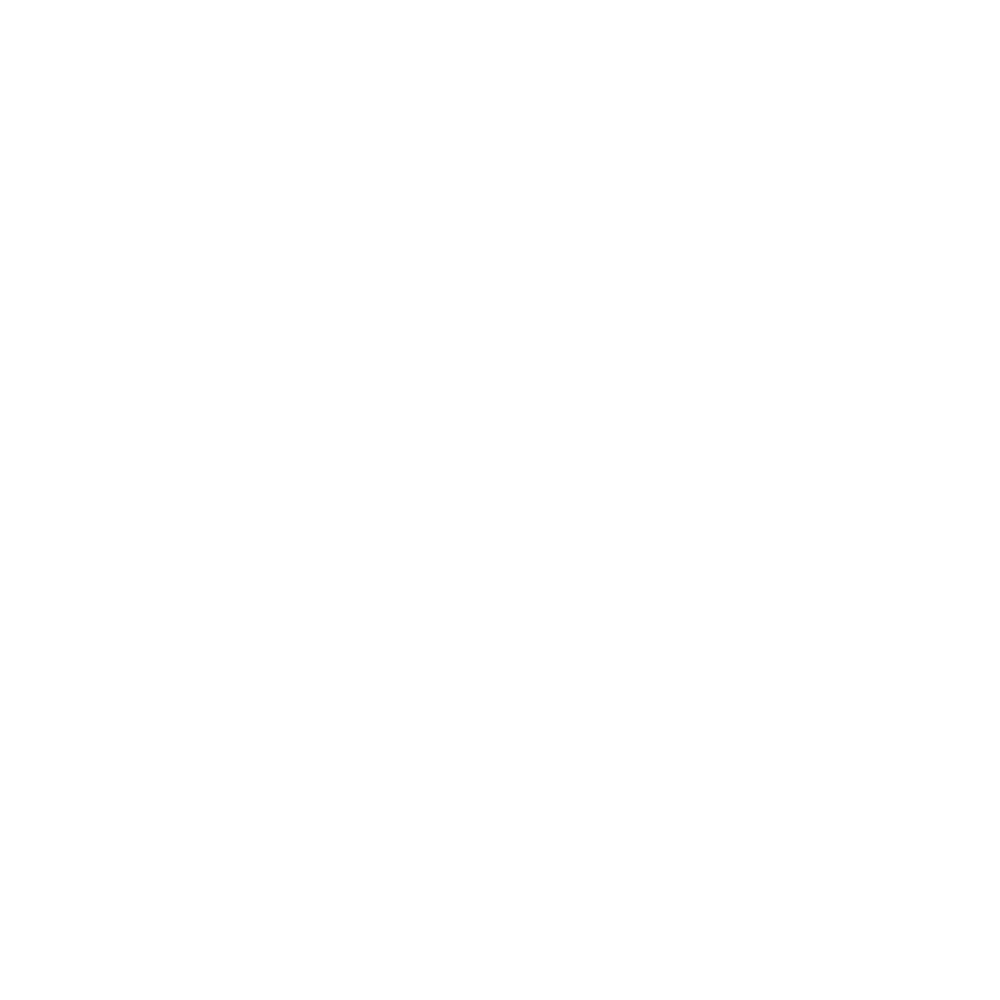
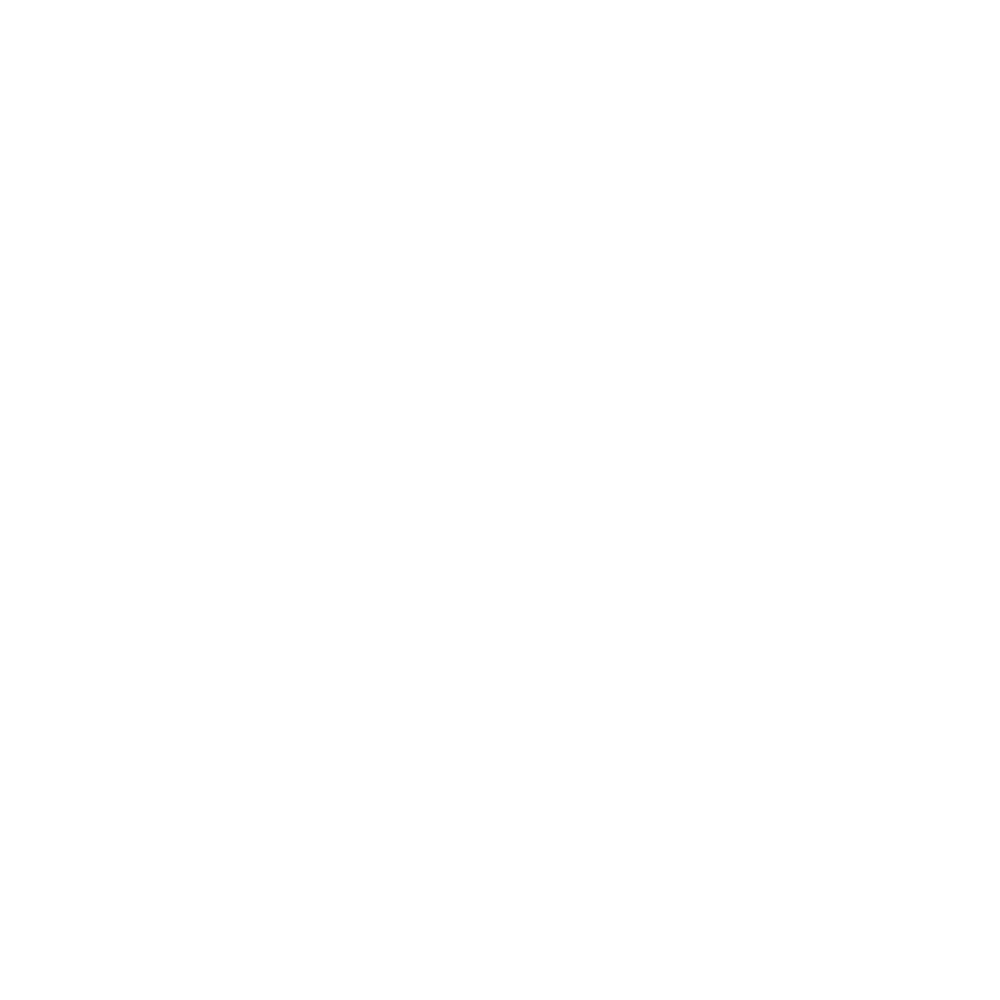
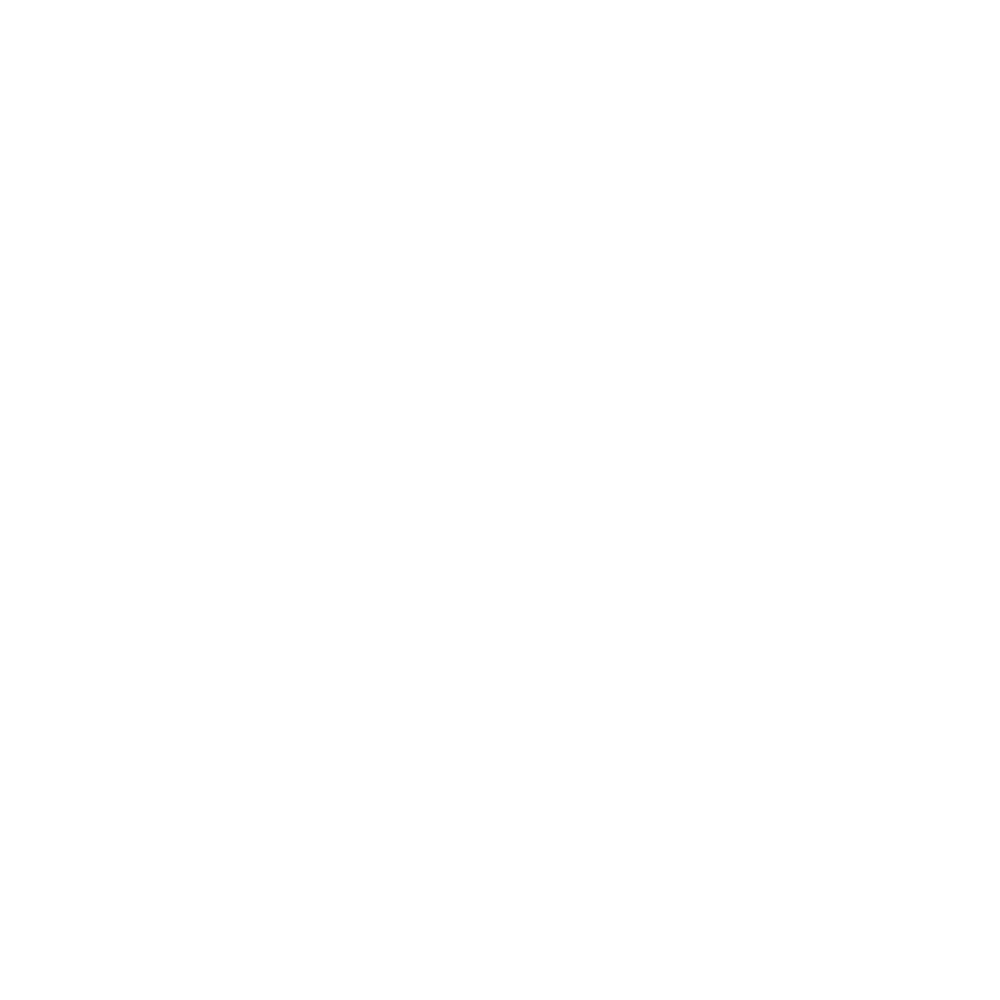
Cleanroom Modules Assembly
At Tonasco, we specialize in manufacturing high-quality cleanroom modules that adhere to ISO-6 cleanroom standards. Our expertise extends to producing complete sub-modules requiring mechanical, electrical, and pneumatic assembly.
Drawing from our extensive experience in the Semiconductor, Optical, Medical, and Diagnostics industries, we deliver meticulously cleaned and rigorously tested submodules and cleanroom modules tailored to our customers’ exact specifications. Our streamlined “plug and play” solutions not only save time and resources but also mitigate risks for our clients.
Our comprehensive approach simplifies the sourcing process for our customers, particularly for production lines or equipment requiring a diverse range of submodules. Leveraging nearly two decades of experience in submodule assembly, we’ve developed reliable and repeatable assembly protocols for both cleanroom and standard submodules, ensuring consistent quality across every product.
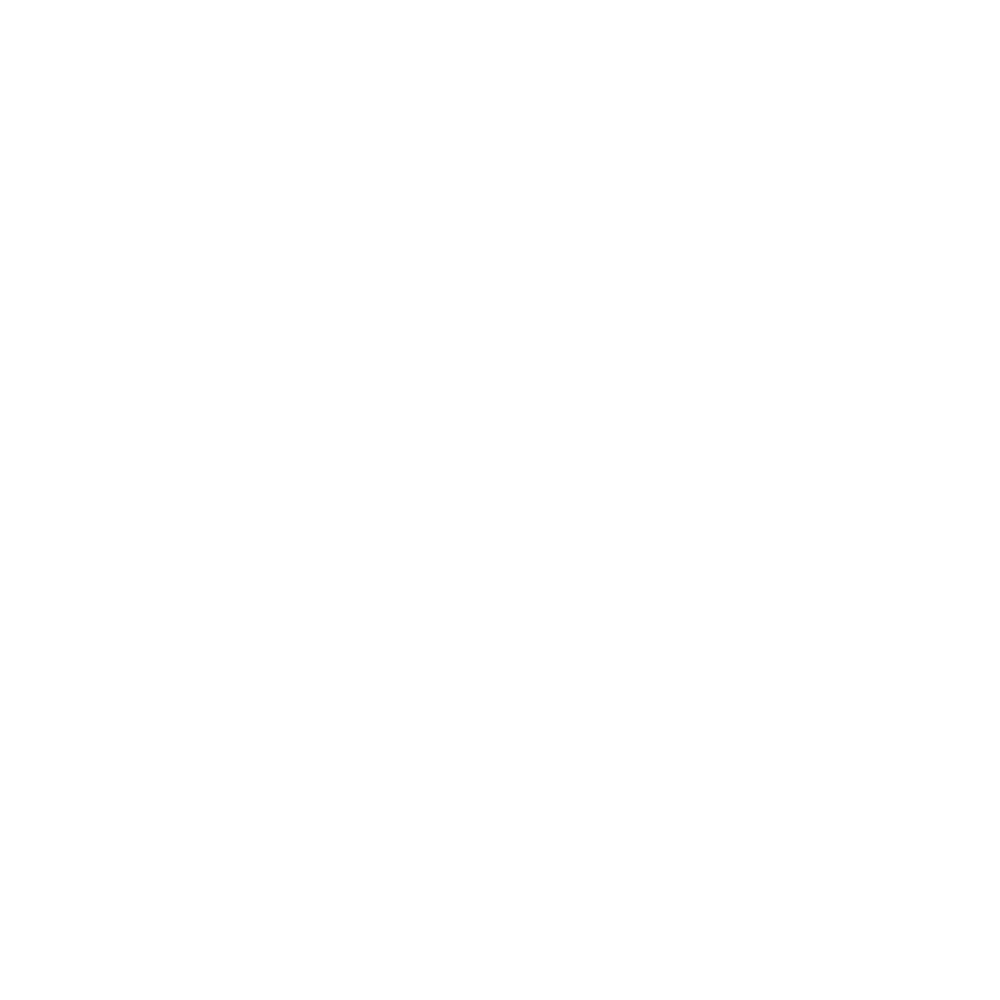
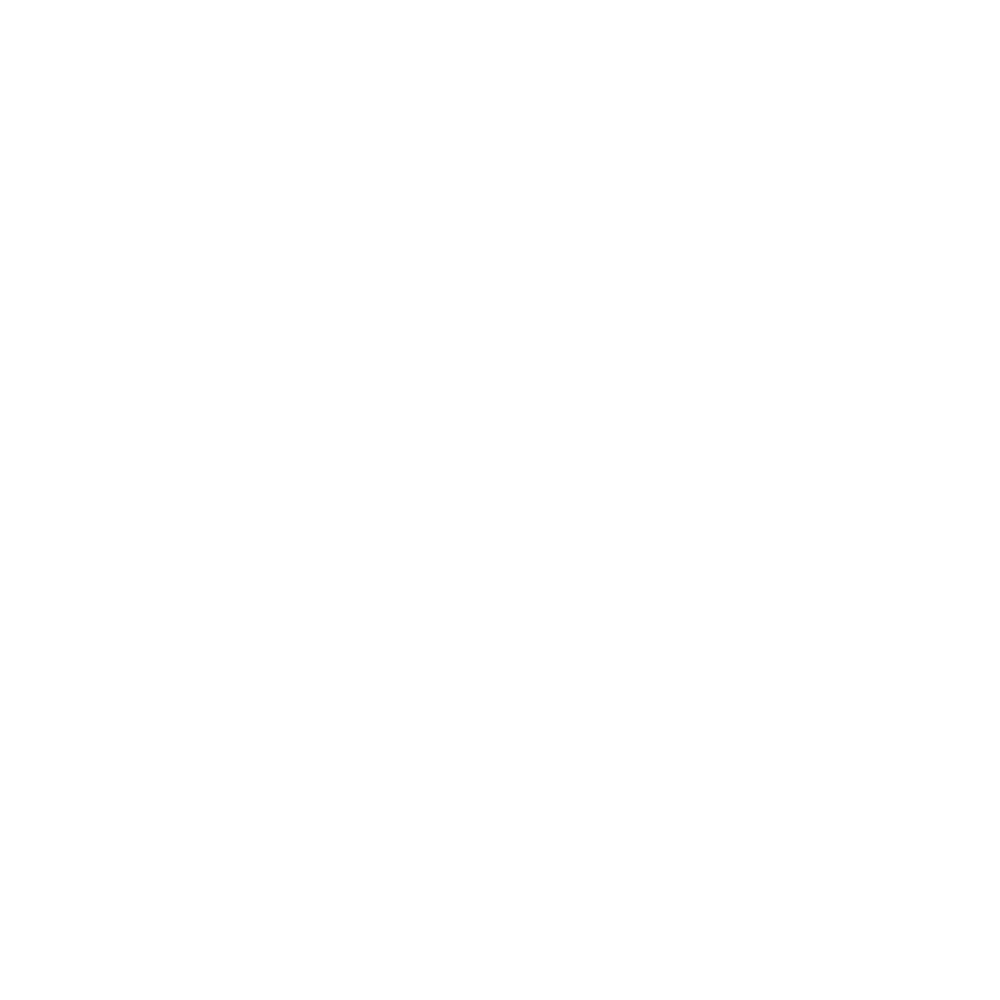
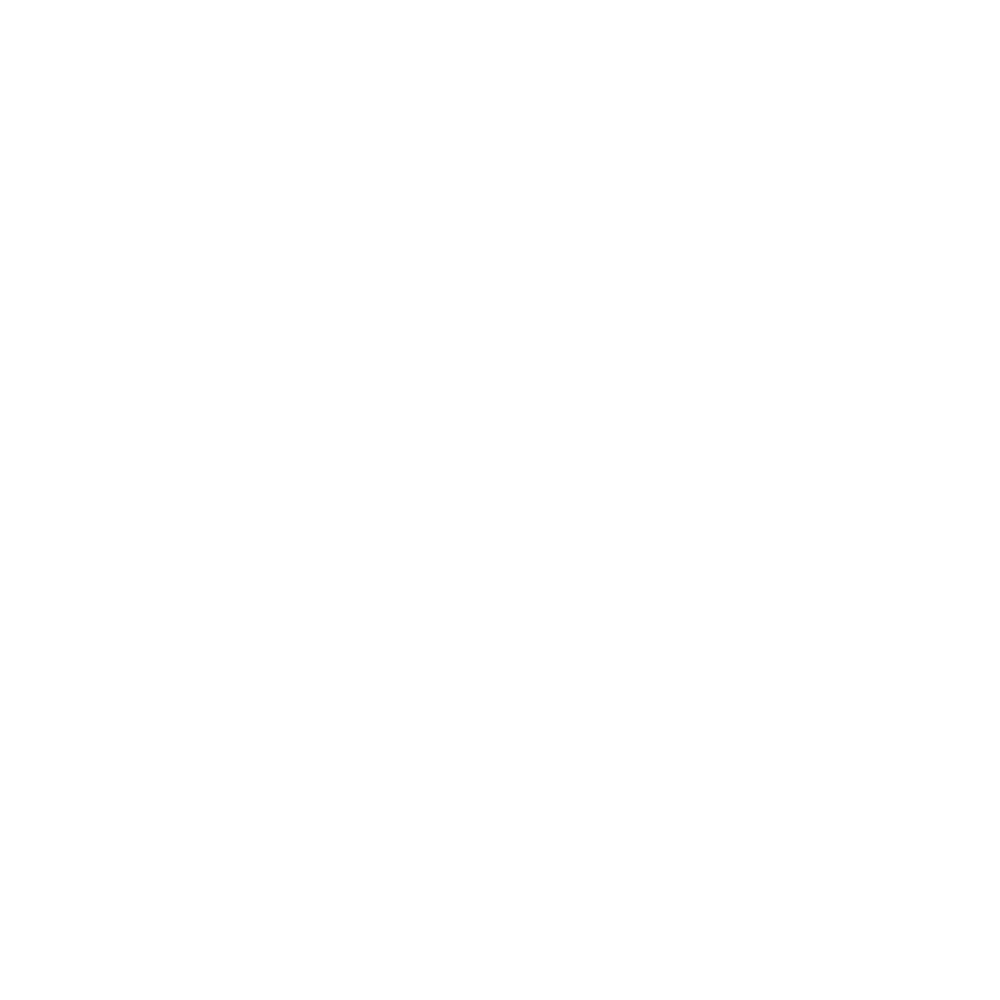
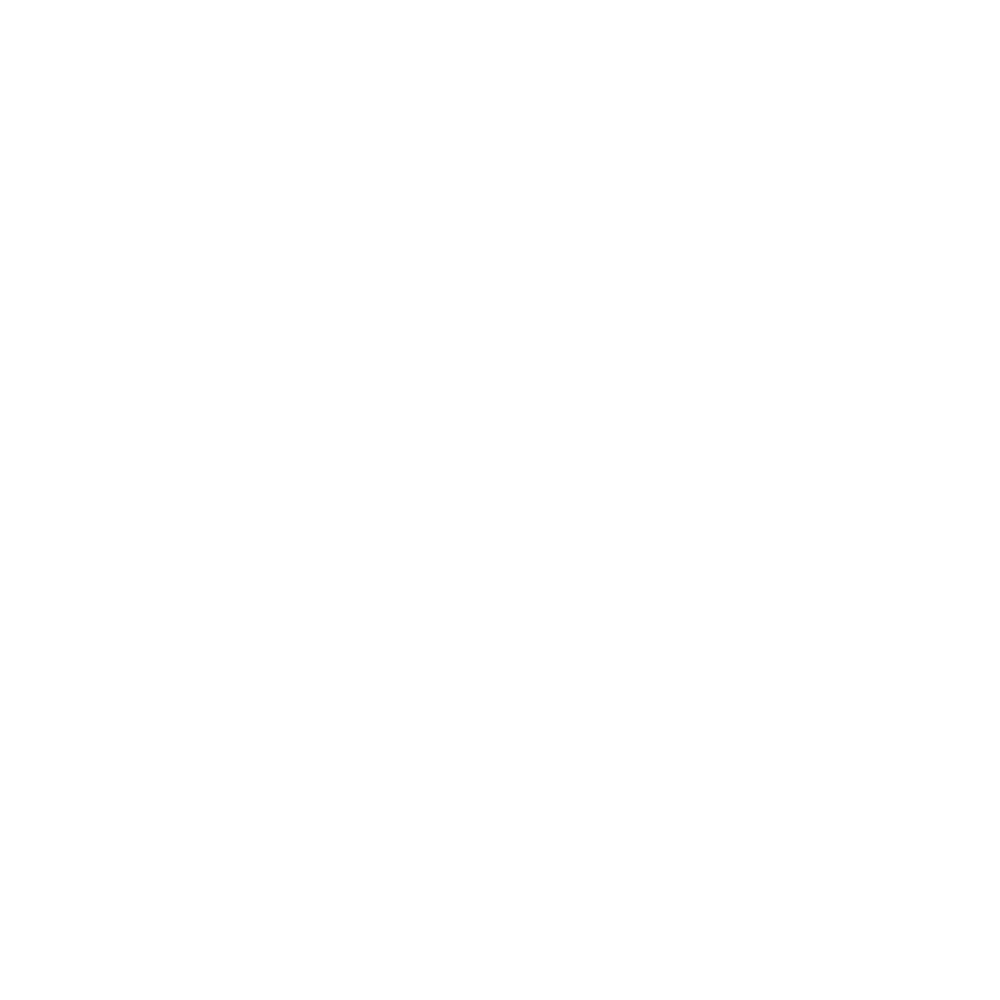
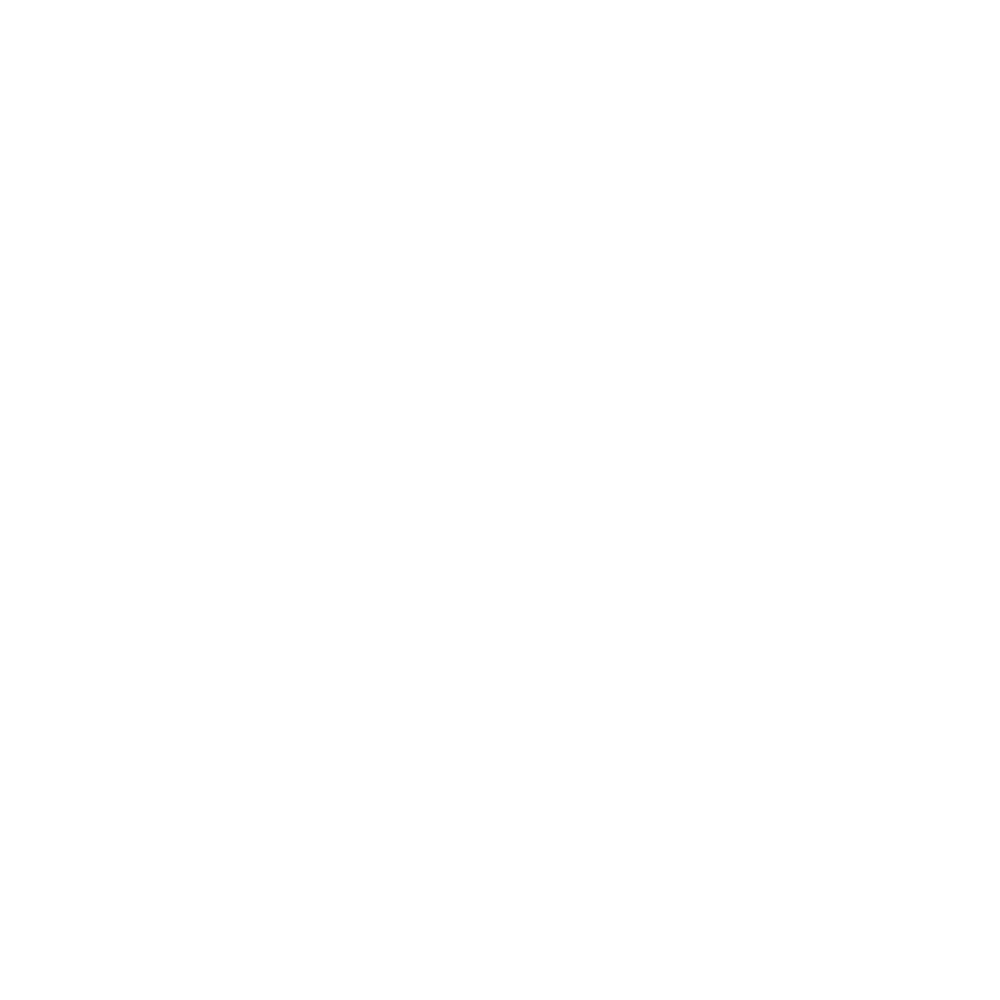
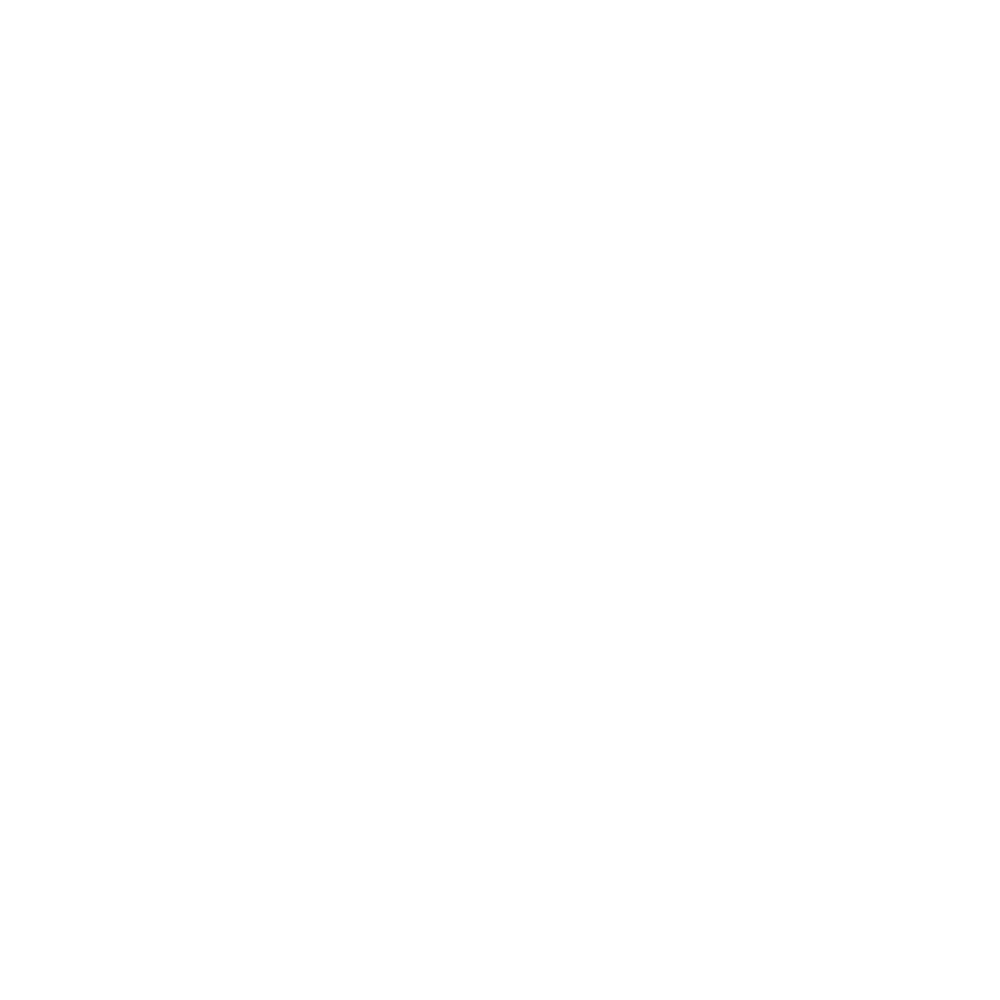
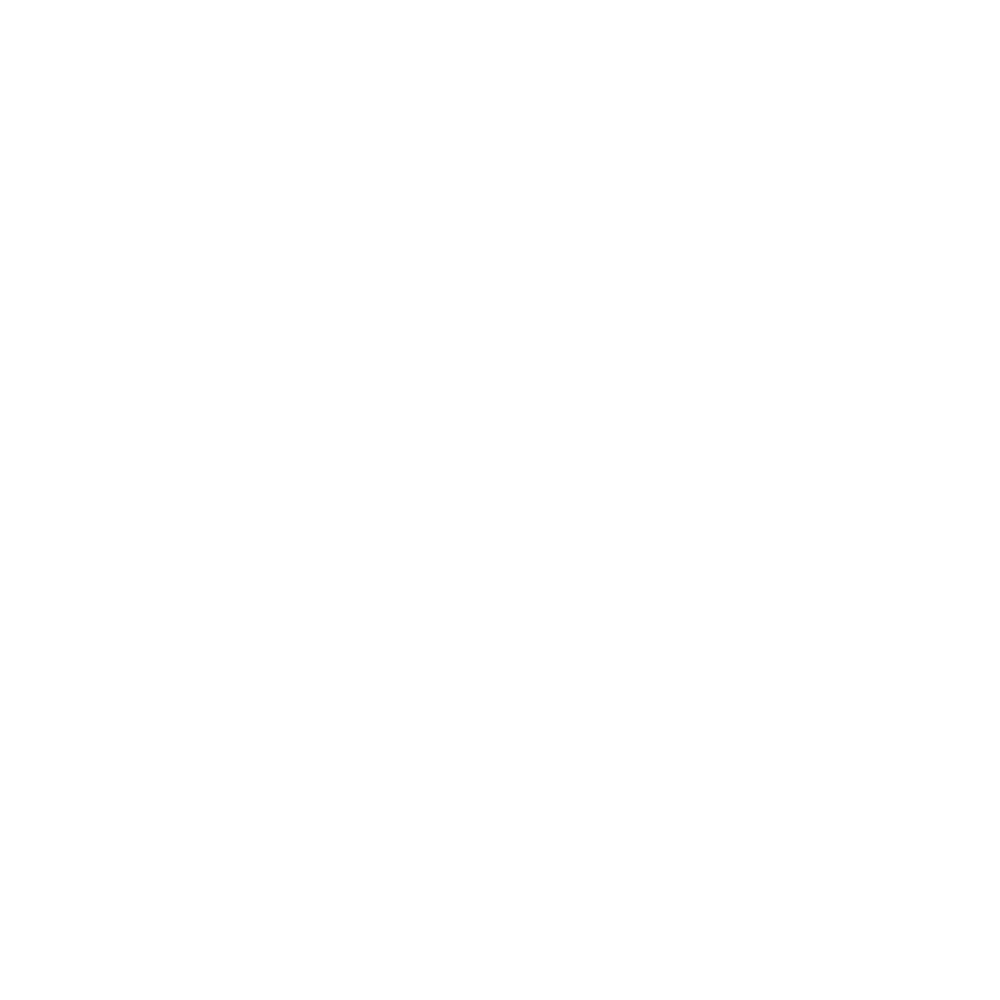
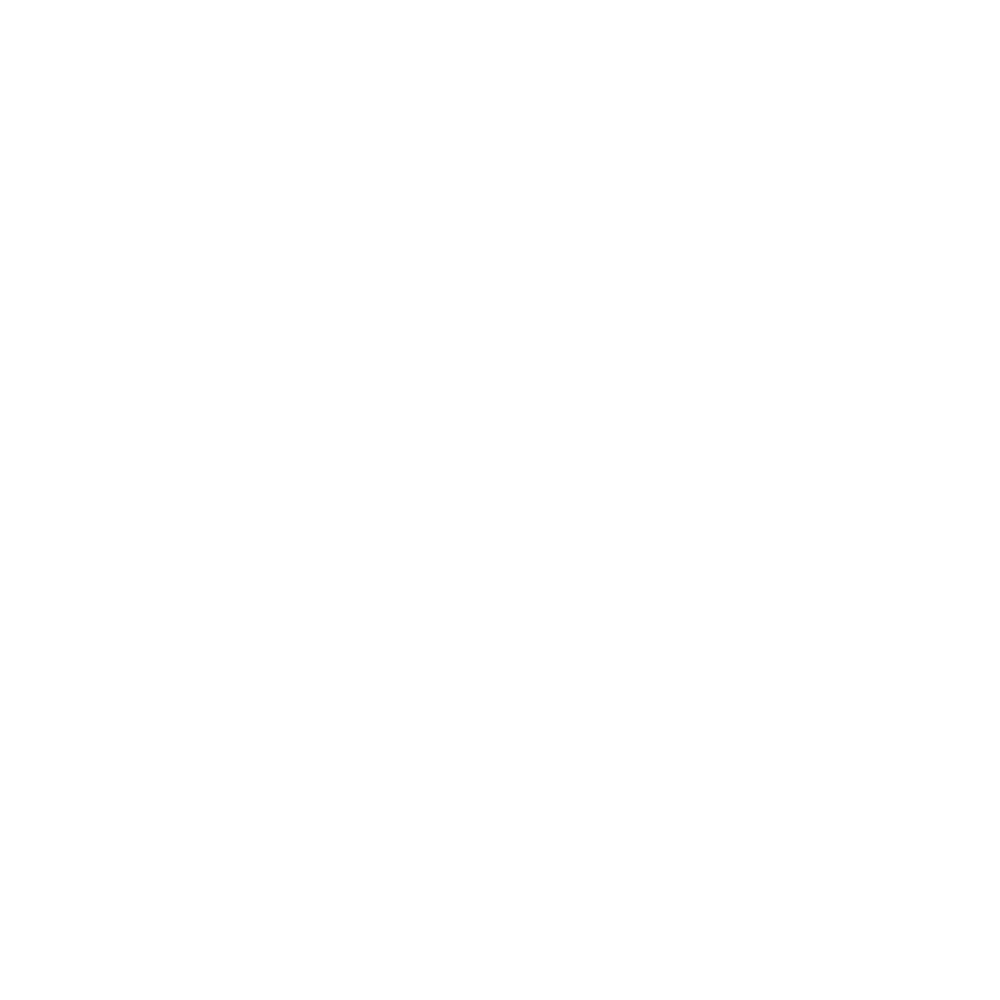
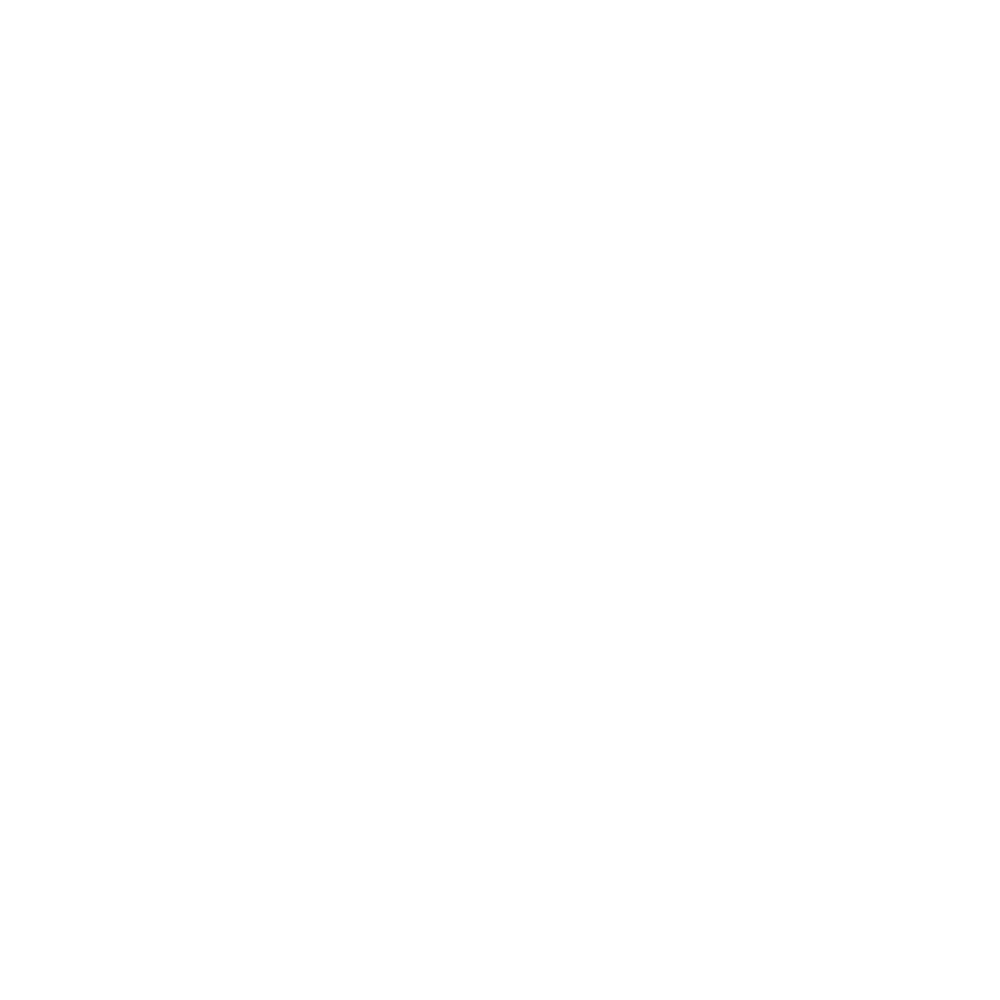