Products
- Home
- Products
High-Mix Low-Volume Precision Components
"High-Mix Low-Volume production is in the DNA of Tonasco, High Precision Machining is our passion!"
At Tonasco, every aspect of our operation is optimized for High-Mix Low-Volume series production of High Precision components. From high-end CNC milling machines and integrated IoT software to our layout and facilities, every element is tailored for efficiency and excellence in precision manufacturing.
Our state-of-the-art Tonasco Smart Factory boasts advanced machinery and cutting-edge machining technologies, including Simultaneous 5-axis CNC Milling Centres, CAM (Computer-Aided Manufacturing), and Simulation Software. These capabilities enable us to meet the most stringent demands for tight tolerance control with precision and reliability.
Superior product quality is our top priority and ultimate commitment to our high-tech clients. Our large team of highly trained QC technicians utilizes high precision QC instruments such as automated Zeiss Coordinate Measuring Machines (CMM) and Visual Inspection Machines. With an ISO9001:2015 certified quality management system and stringent In-Process Quality Control (IPQC) procedures in place, we consistently deliver high-quality components year after year.
Micromachining Precision Components
Micro-milling is at the heart of our expertise. From crafting micro-grippers and surgical robot parts to manufacturing medical-grade plastic gears, we specialize in producing high-quality micro-components ranging in size from 5 to 10mm, with precision tolerances as tight as ±0.005mm.
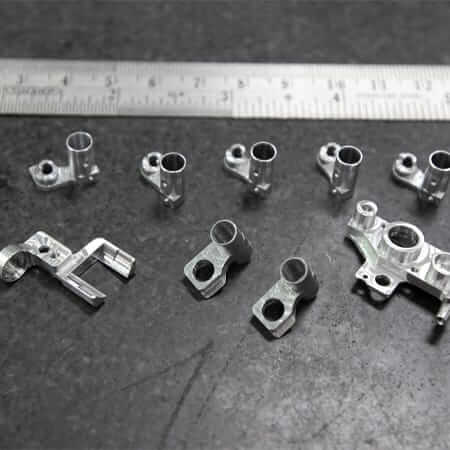
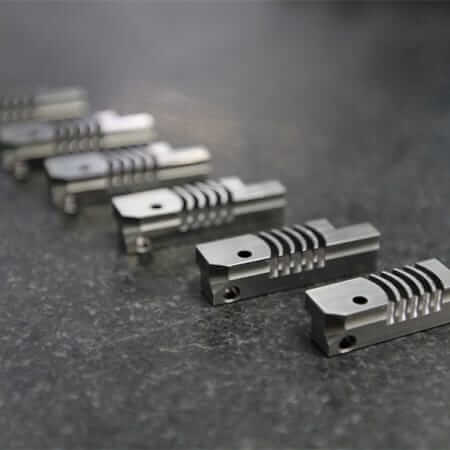
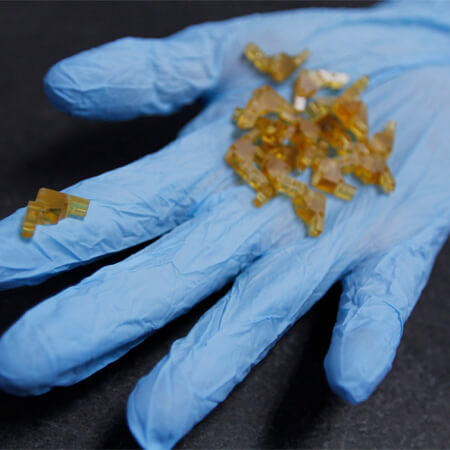
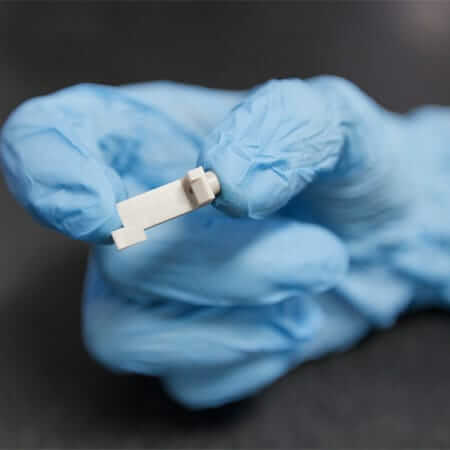
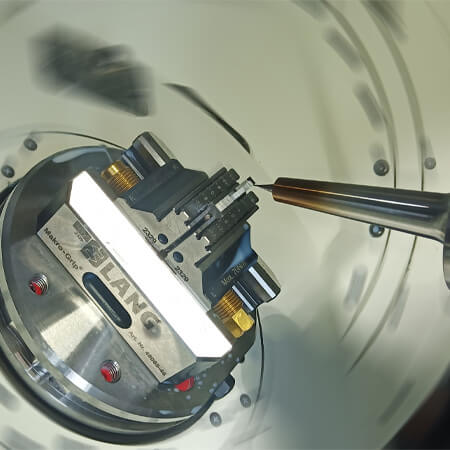
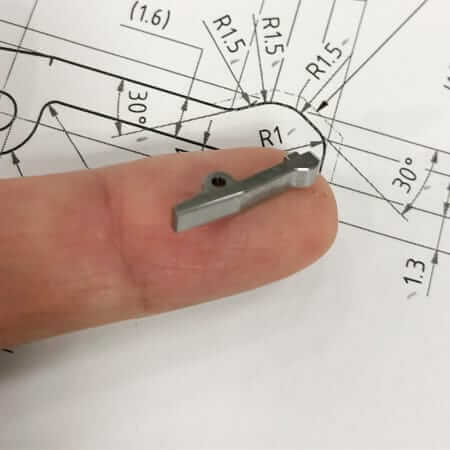
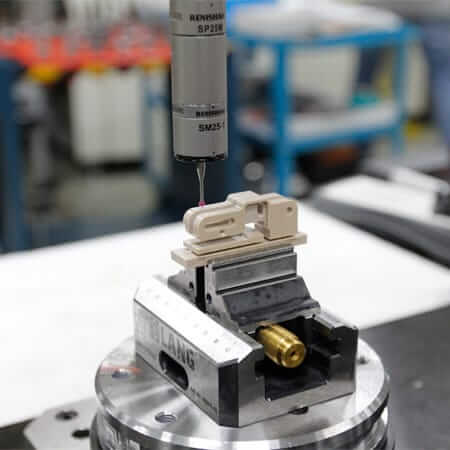
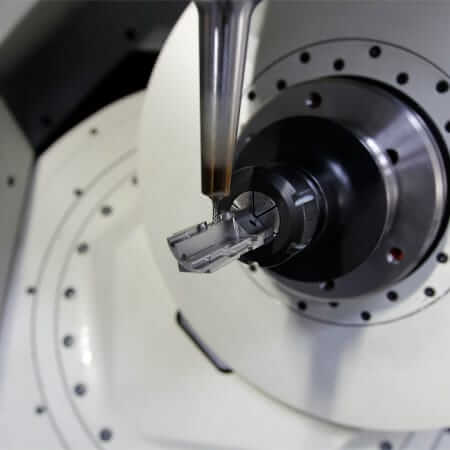
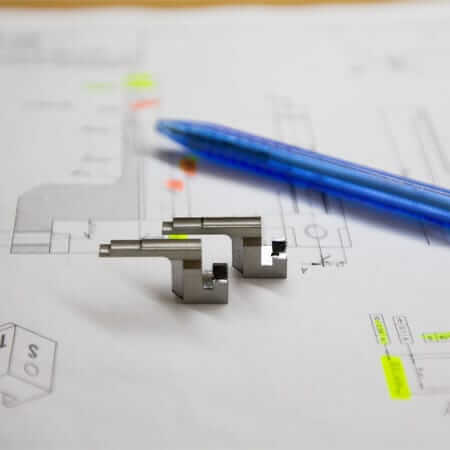
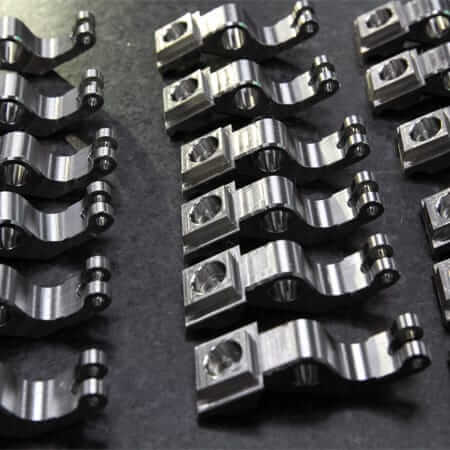
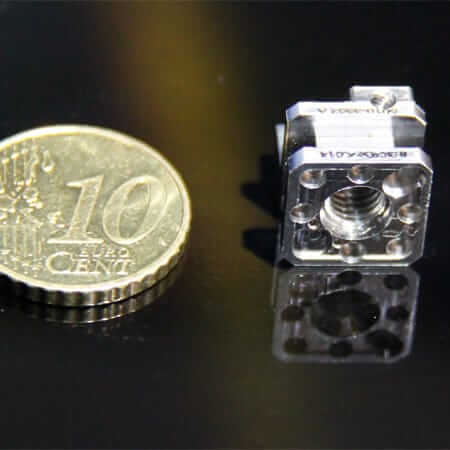
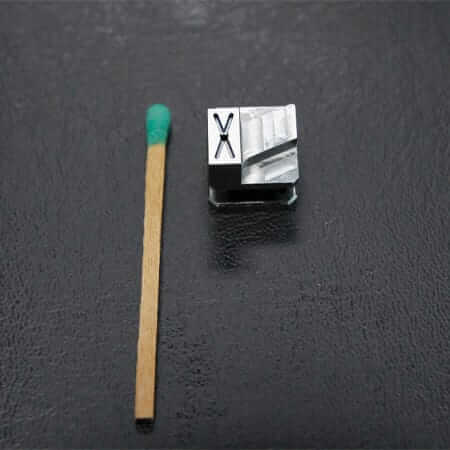
Complex Precision
Components
Achieving excellence in complex machining goes beyond having top-of-the-line 5-axis CNC milling machines or cutting-edge CAM and Simulation software.
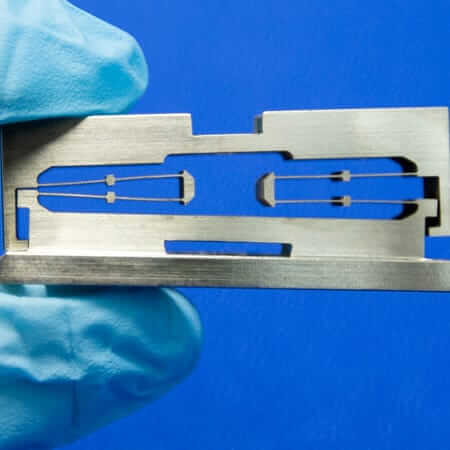
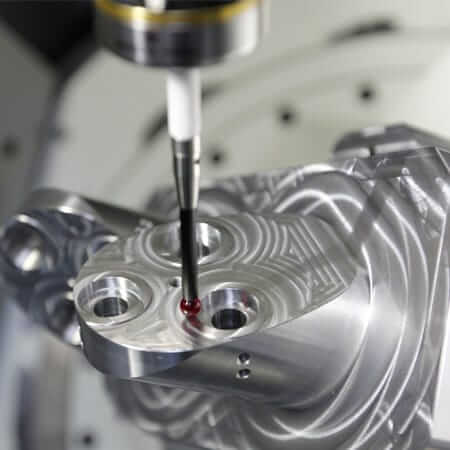
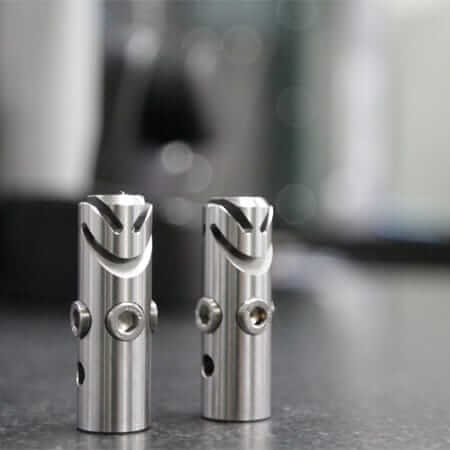
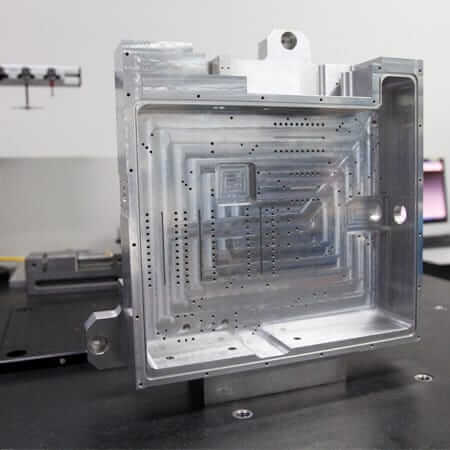

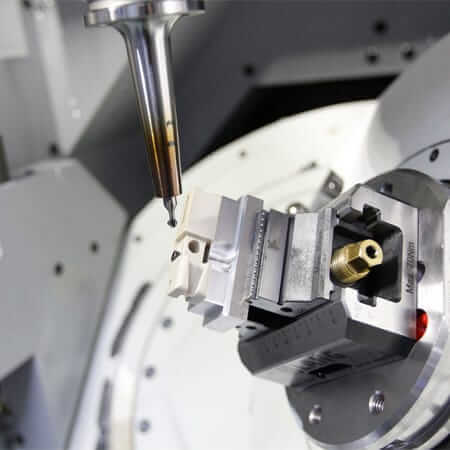
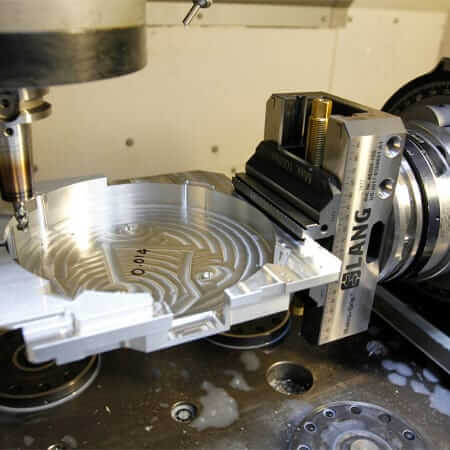
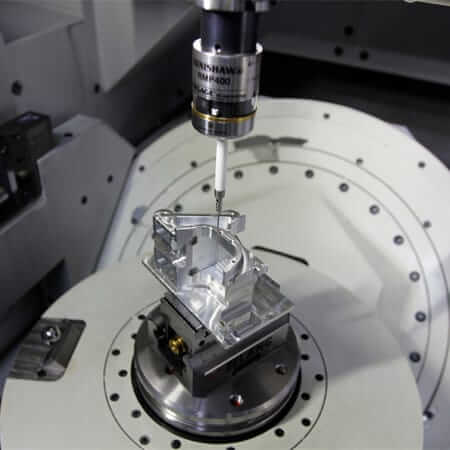
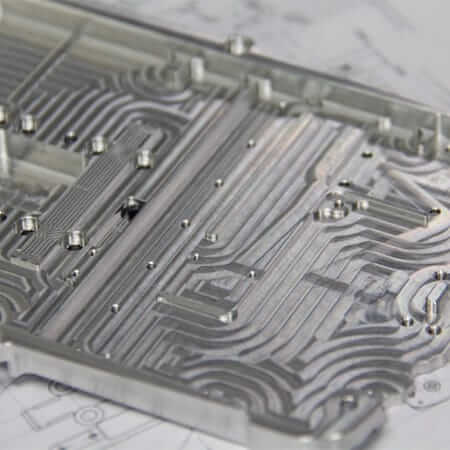
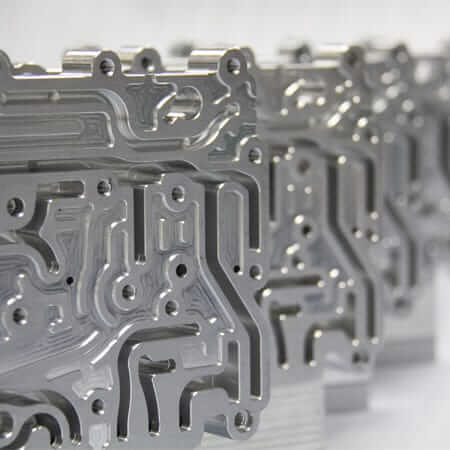
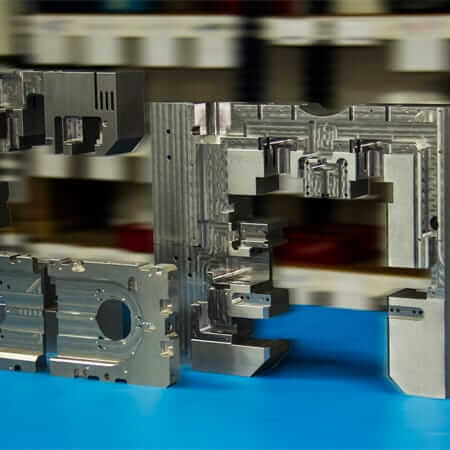
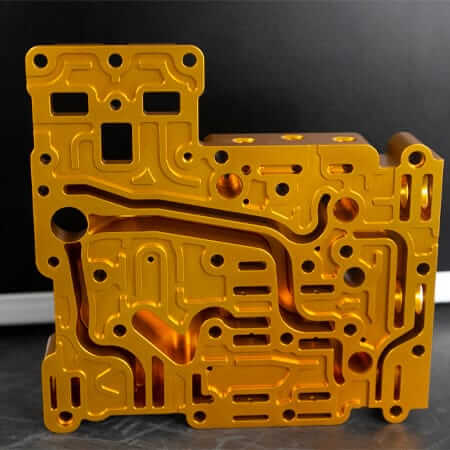
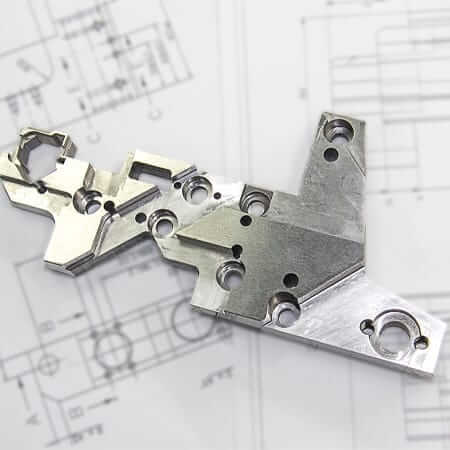
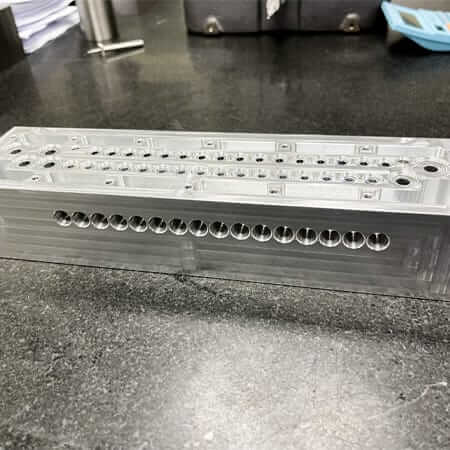
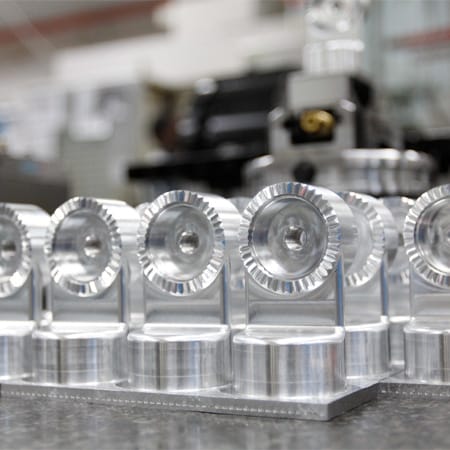
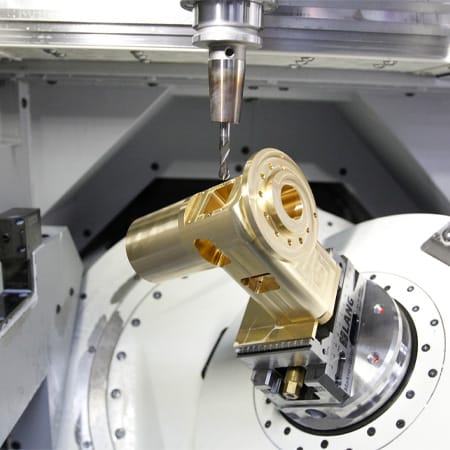
Cleanroom Precision
Components
At our facilities, we specialize in producing clean components that meet ASML Grade 2 cleanliness standards. Our expertise extends to clean production techniques tailored to the Semiconductor, Optical, Medical, and Diagnostics industries.
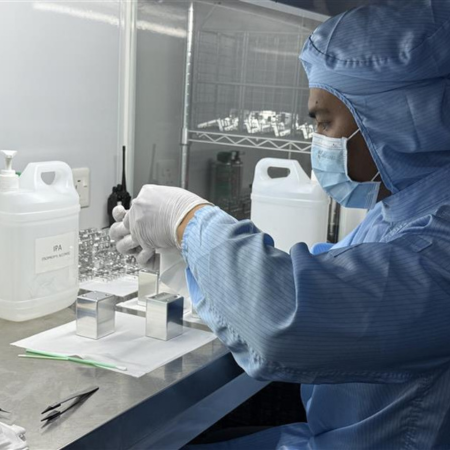
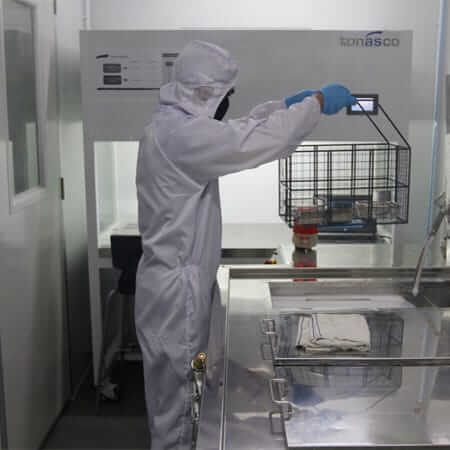
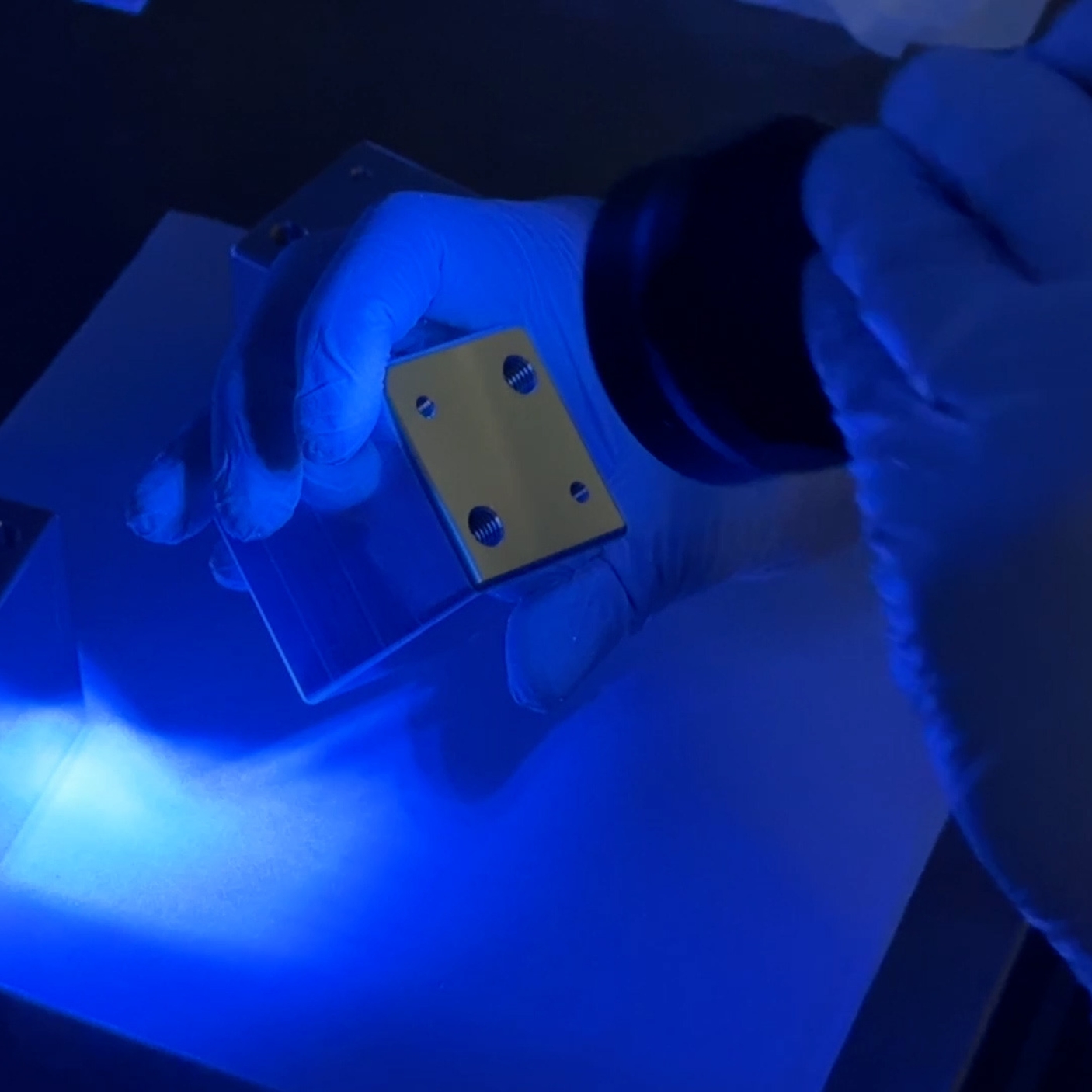
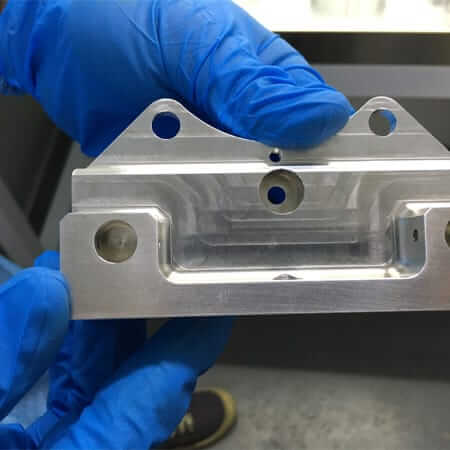
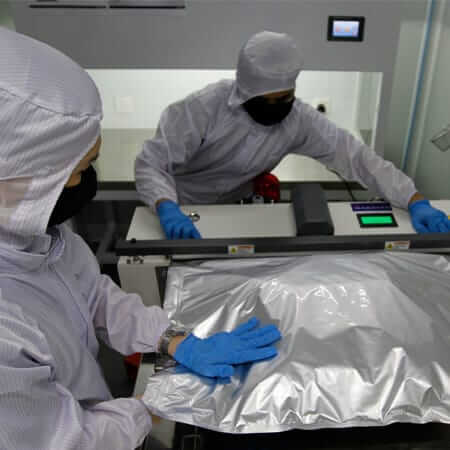
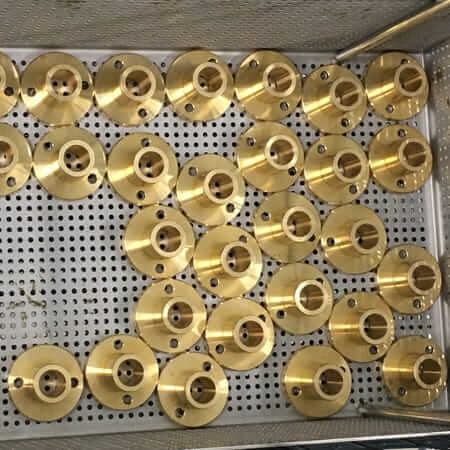
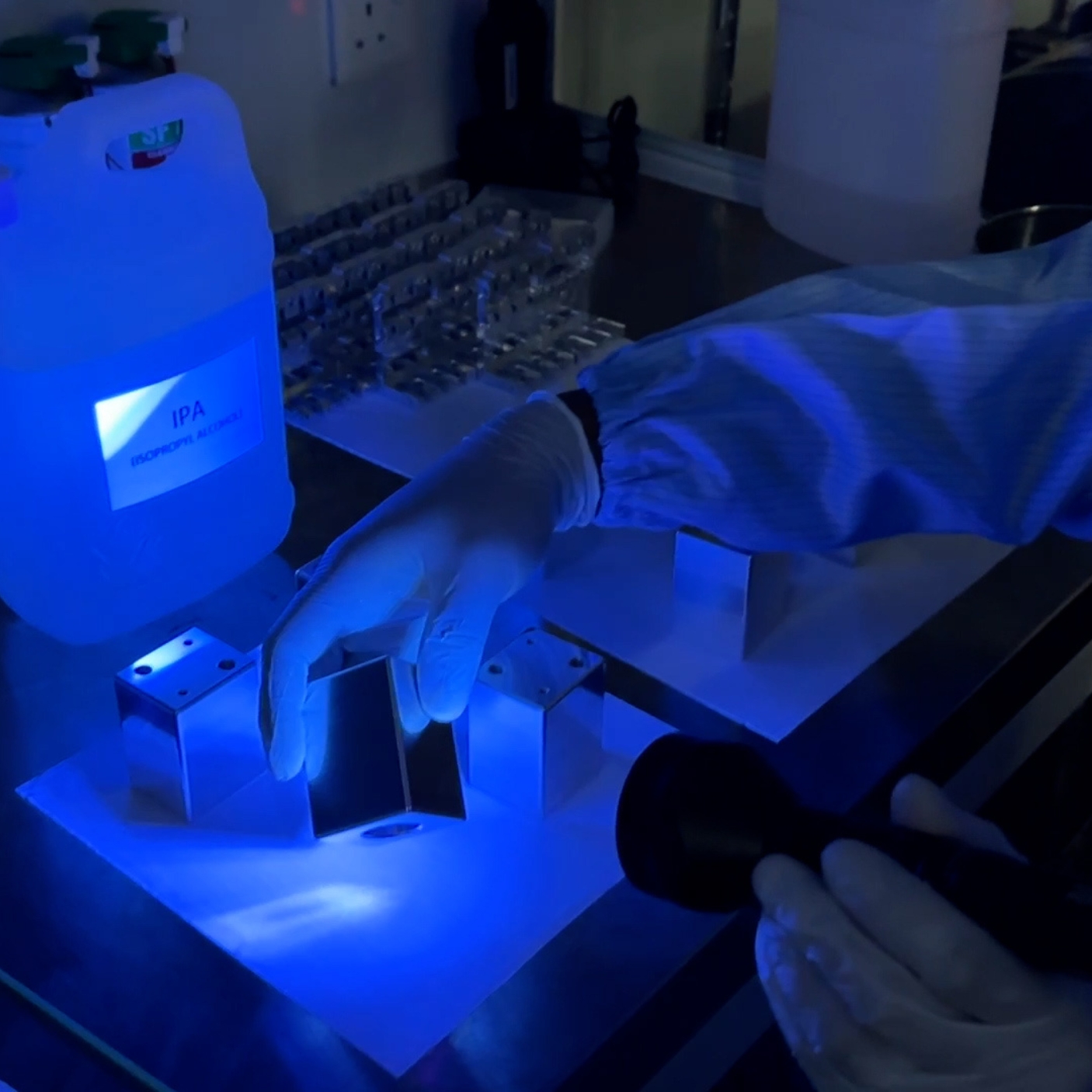
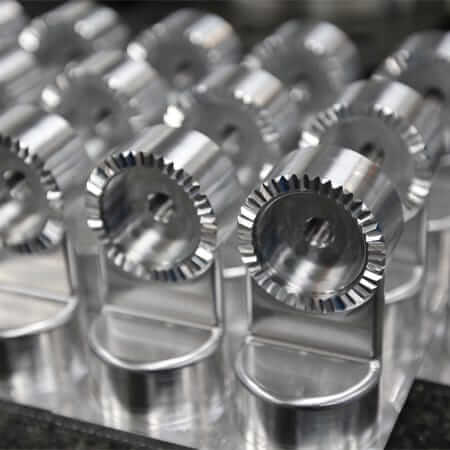
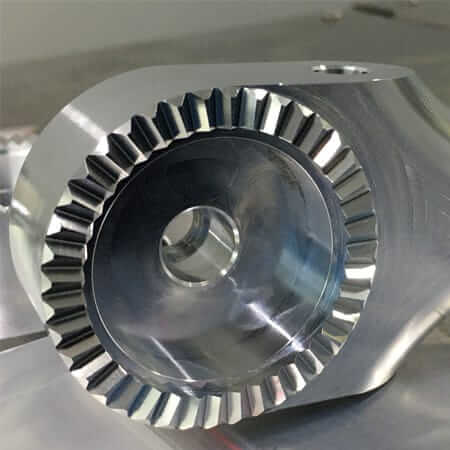
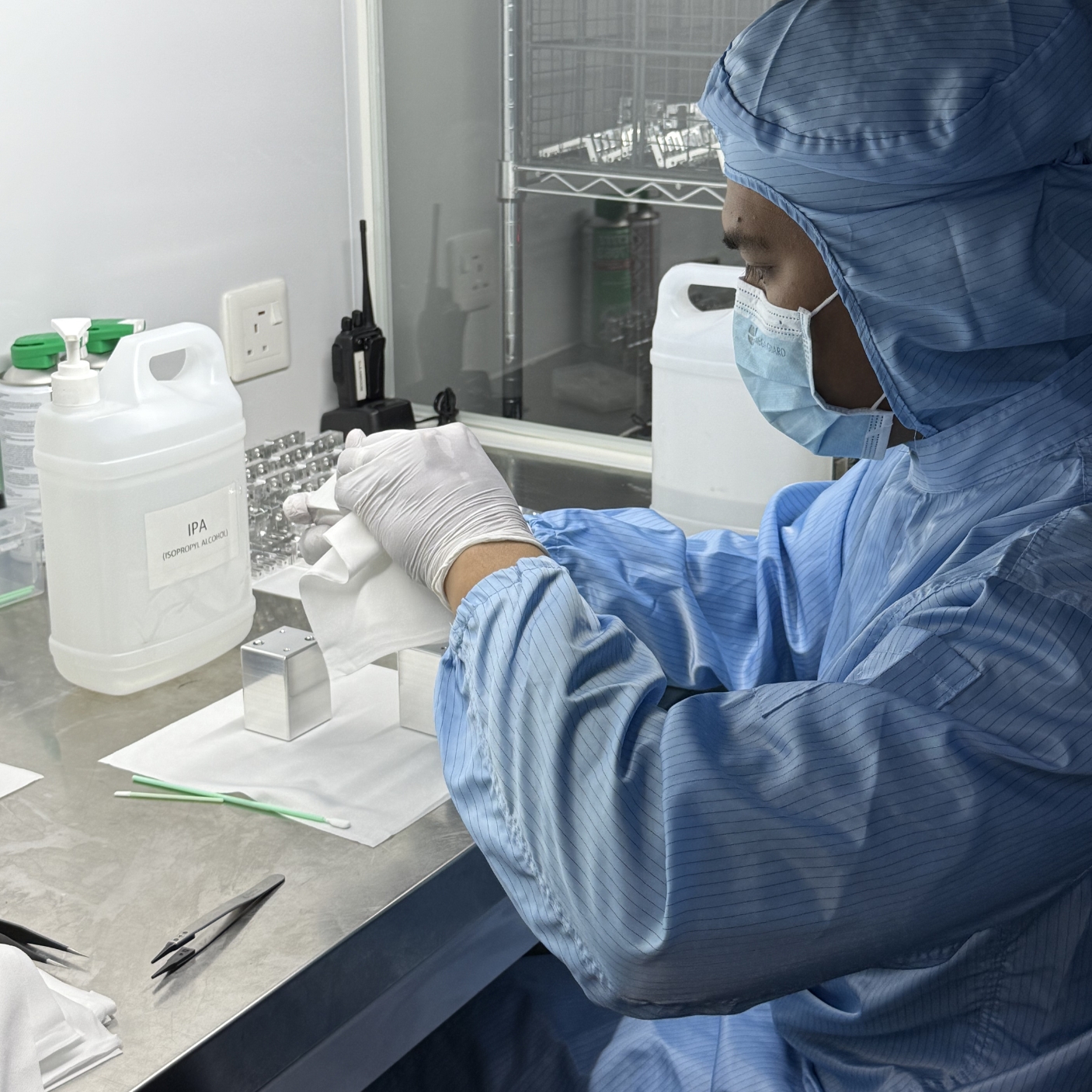
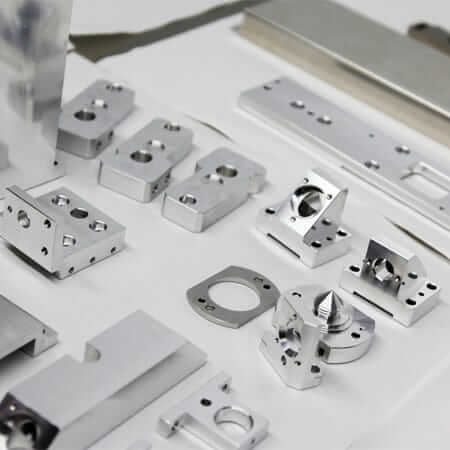
Sub-Modules & Cleanroom Modules Assembly
At Tonasco, we specialize in manufacturing high-quality cleanroom modules that adhere to ISO-6 cleanroom standards. Our expertise extends to producing complete sub-modules requiring mechanical, electrical, and pneumatic assembly.
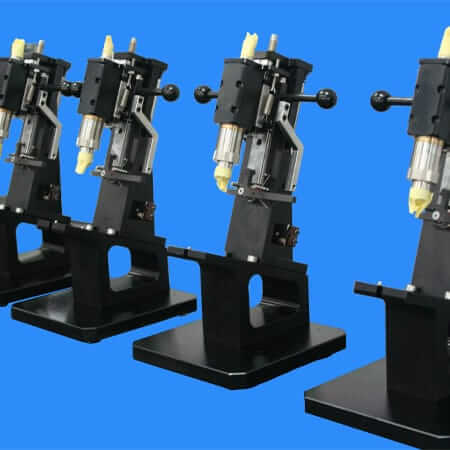
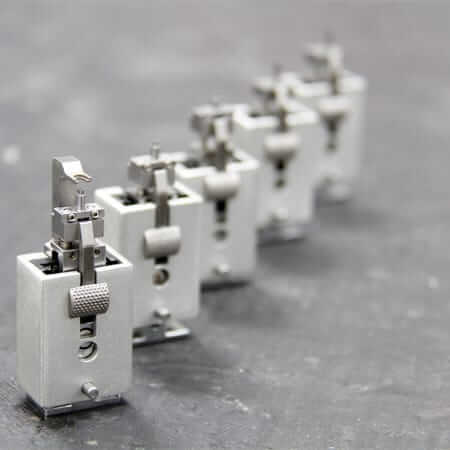
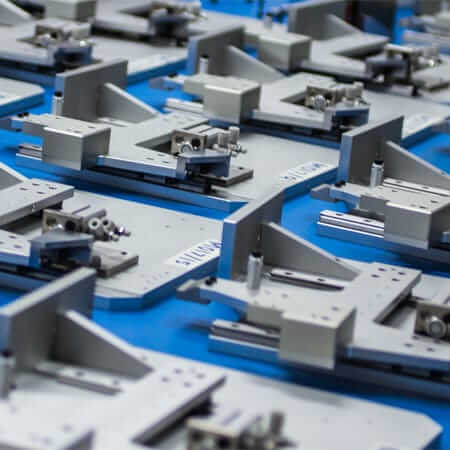
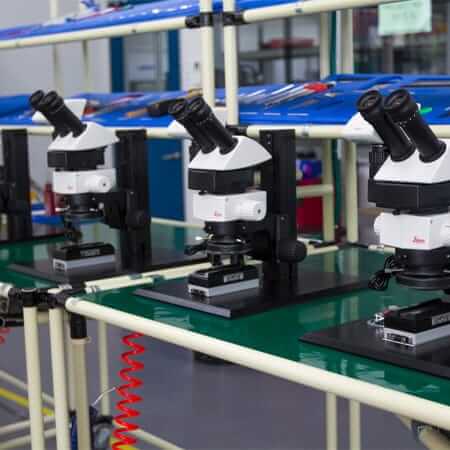
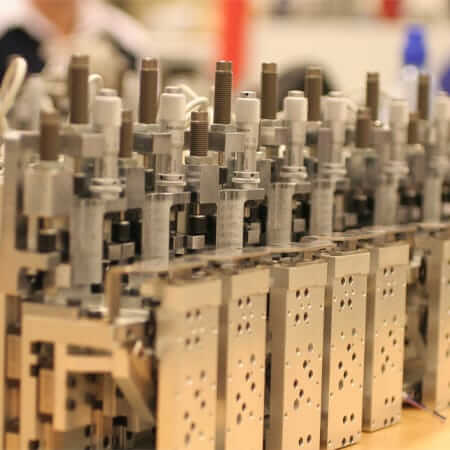

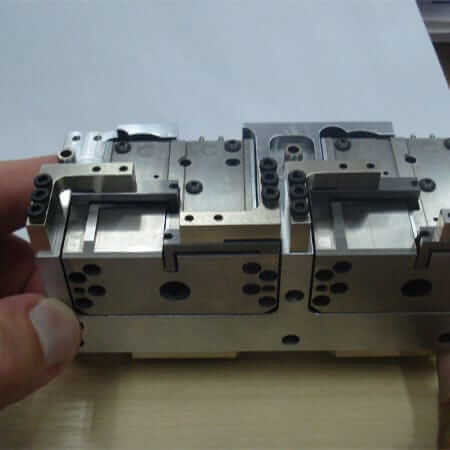
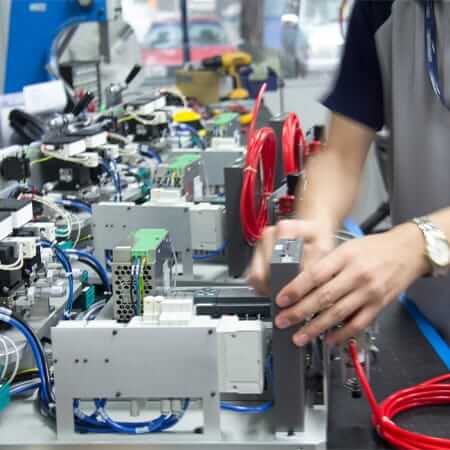
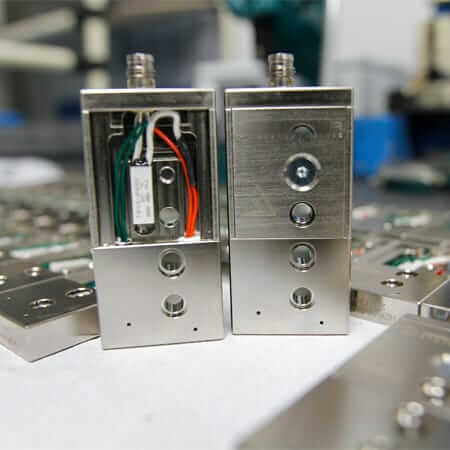
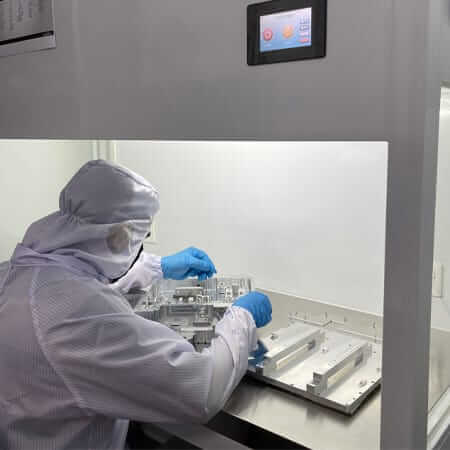